Injection Moulding Service
Machined prototypes and production parts delivered on time
CERTIFICATIONS
RenderFact Injection Moulding
Plastic injection molding is the most widely used manufacturing technique to produce mass units of plastic parts that serve industrial and commercial purposes. Plastic injection molding also has the highest range of materials, color, and configuration when put side-by-side with processes like CNC machining or Additive manufacturing. In Injection molding molten resin is injected under high pressure into the cavity of a metal die and then rapidly cooled, forming a solid shape. A single cycle to make a finished part may take anywhere from a few seconds to minutes depending on part complexity and size.
At Renderfact we specialize in producing high-quality plastic injection molded parts and mold tools. With Advanced material verification and quality processes, we can ensure your tools and parts exceed your expectations. Using the technical maturity to produce high quality custom plastic molded parts for defense, automotive, medical, aerospace and consumer products.
If you are ready to start your next project, upload your product design information for a competitive injection molding quote today.
Below are some of the benefits of Injection molding and How it Works!
Advantages of Injection Moulding
Quality and Detail
Scalability and repeatability
Cost-effectiveness
Material diversity and options
Low-volume manufacturing
Custom Surface Finish
INJECTION MOULDING
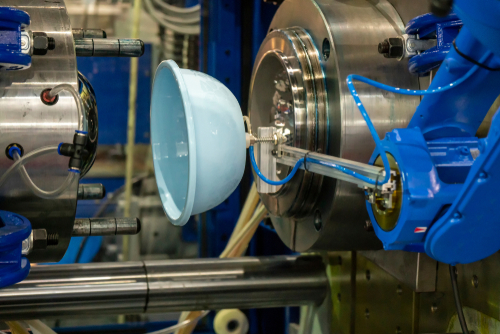
Renderfact specializes in the use of rapid prototyping and mass-manufacturing techniques to produce high-end plastic injection molded parts and mold tools. Our plastic injection molding process can make custom prototypes and end-use parts in as quick a week. At Renderfact, cost-efficiency is optimized by using aluminum mold tooling that can reproduce thousands of parts and accelerate your product development cycle.
The injection molding process essentially involves loading of resin pallets into a barrel where they will eventually be melted, compressed, and injected into the mold’s runner system. Hot resin is shot into the mold cavity through the gates and the part is molded. Ejector pins facilitate removal of the part from the mold where it falls into a loading bin. Molded parts can be finished in many ways that may cover purely aesthetic finishes or offer some form of protection to the part. Finishes should beautify and enhance the sophistication and functionality of any part.
Materials
Injection Moulding can be done on plastics such as ABS, PP, PVC, PE, HDPE, Nylon, PC, PU, PEEK, PC/ABS, POM, PMMA
ABS
High impact resistance, low-cost & low density.
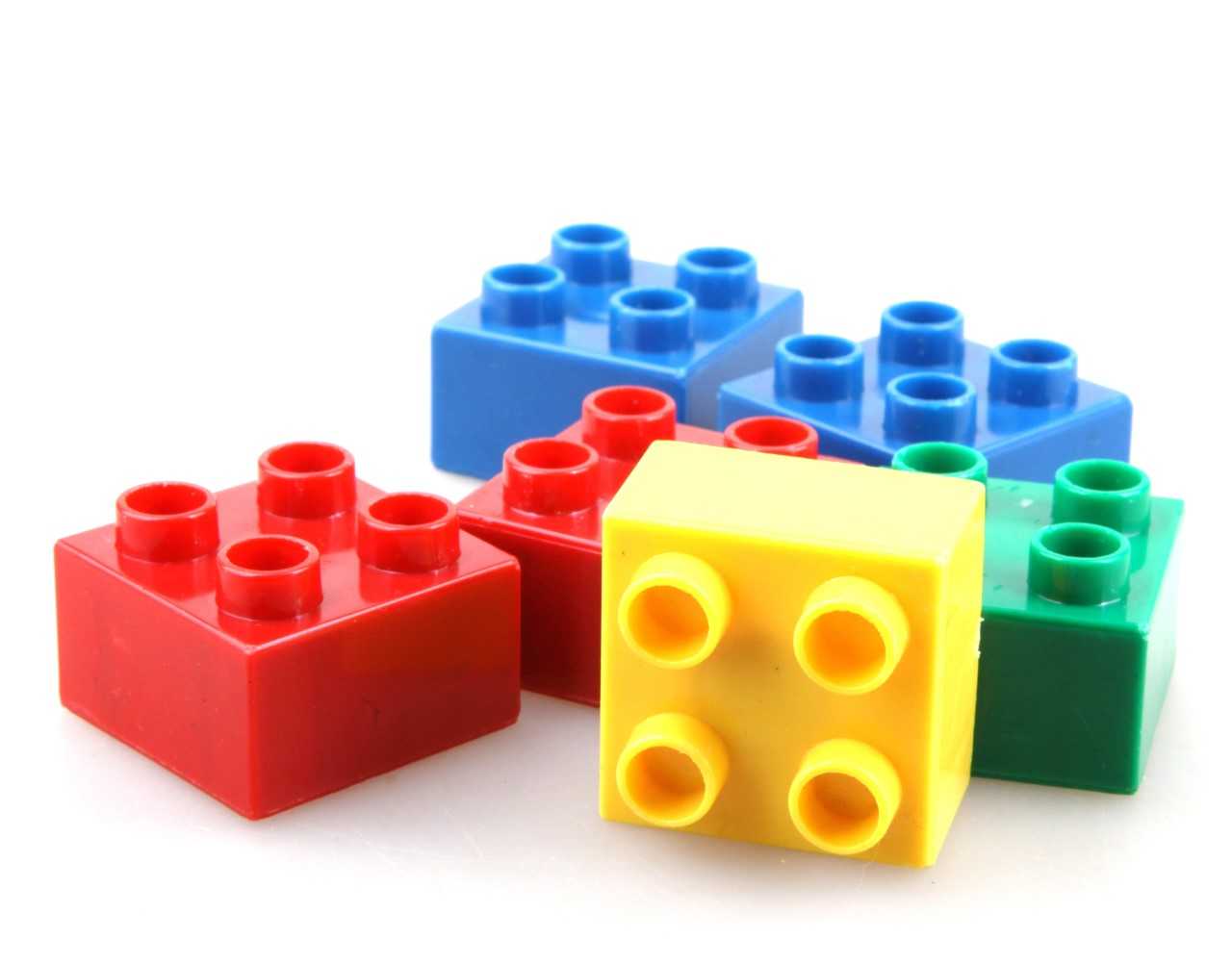
Polypropylene
Polypropylene (PP) is the most common Injection molding plastic. Excellent chemical resistance. Food-safe grades available.
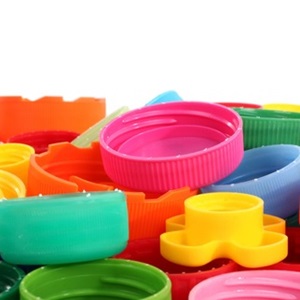
PVC
PVC is the third most used plastic with all-around good mechanical properties, excellent chemical and weather resistance and good toughness.
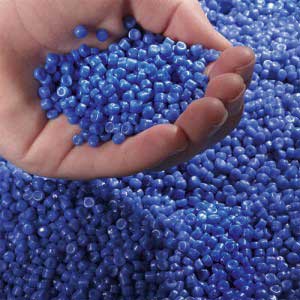
Polystyrene
Polystyrene (PS) is the injection molding plastic with the lowest cost. Food-safe grades available. Not suitable for mechanical applications.
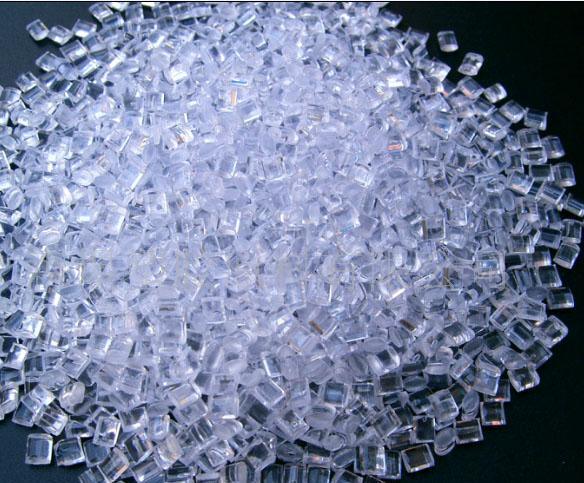
Polyethylene
Lightweight thermoplastic with good impact strength & weather resistance. Suitable for outdoor applications.
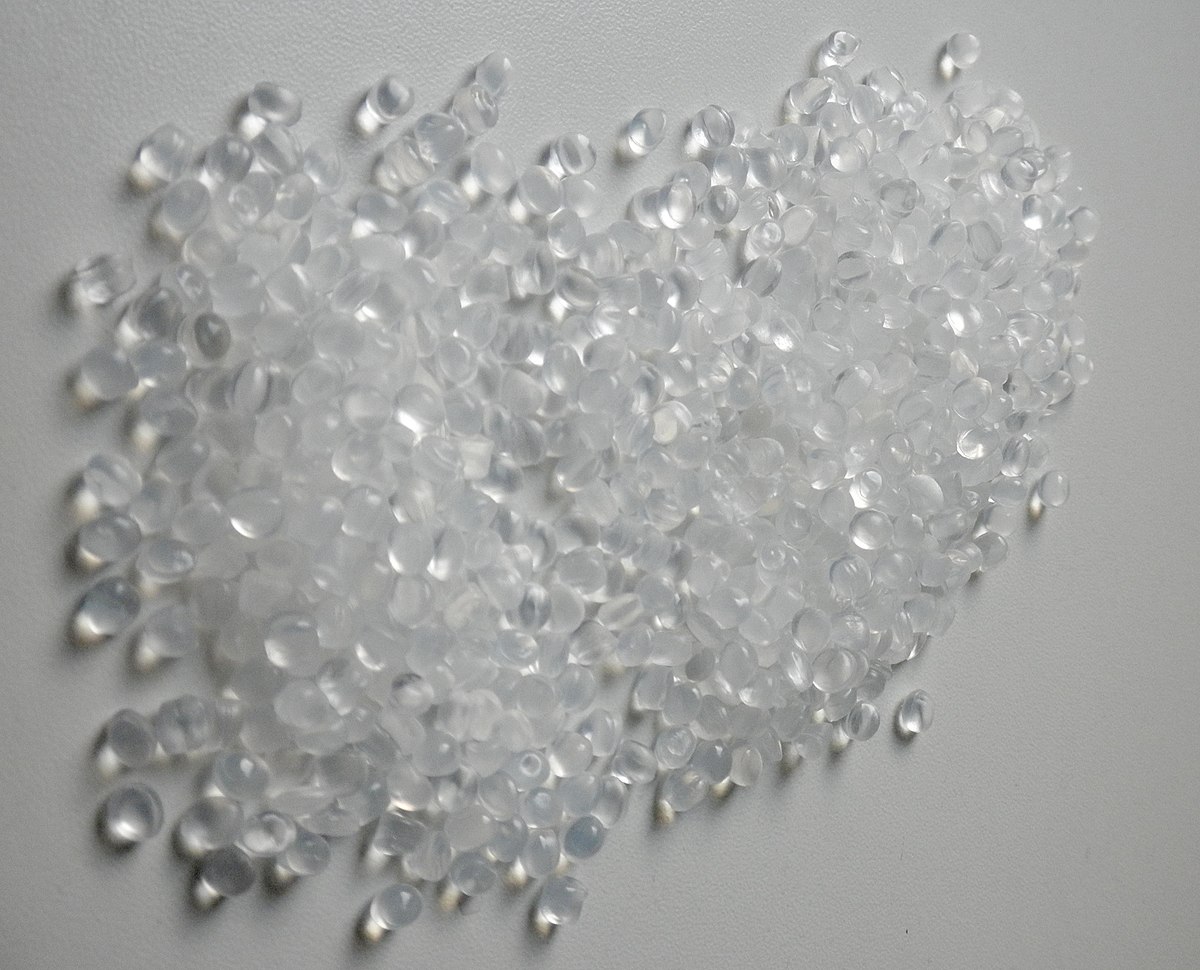
HDPE
Excellent strength-to-weight ratio, impact and weather resistant.
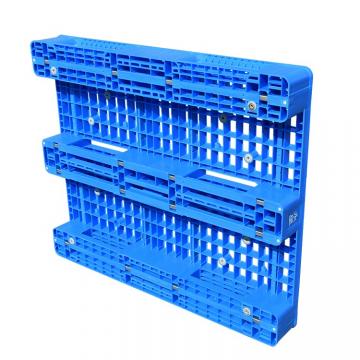
Nylon
Engineering thermoplastic with excellent mechanical properties and high chemical & abrasion resistance. Susceptible to moisture.
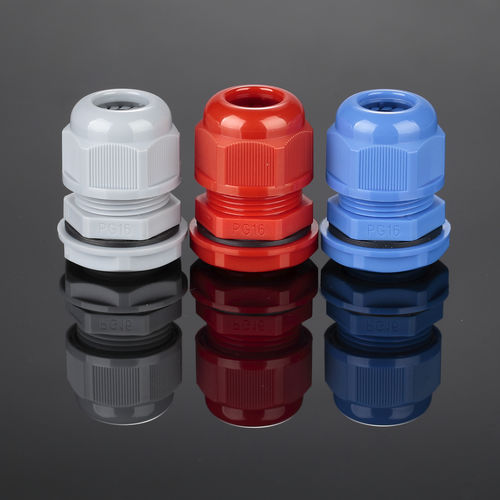
Polycarbonate
High thermal resistance, weather resistance & toughness.
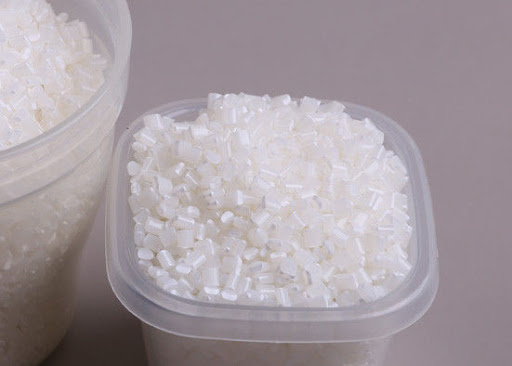
Polyurethane
High impact strength and good mechanical properties & hardness. Thermoplastic with high impact strength and good mechanical properties & hardness. Suitable for molding parts with thick walls.
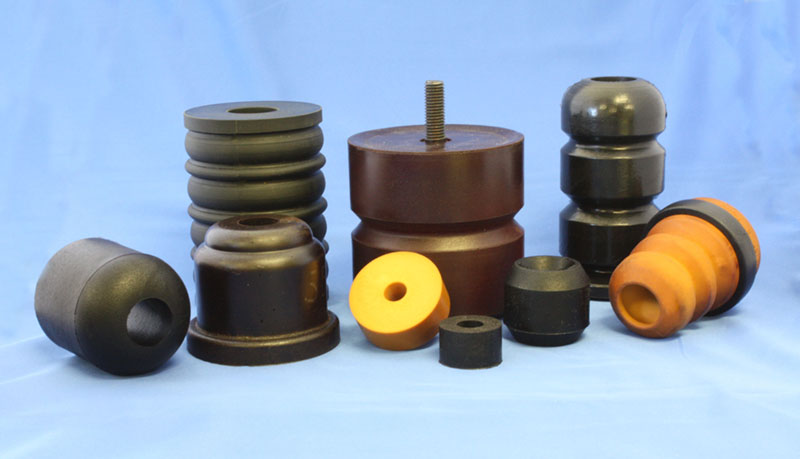
PEEK
High-performance engineering thermoplastic with excellent strength and thermal & chemical resistance. Used to replace metal parts.

PC/ABS
Blend of two thermoplastics resulting in high impact strength, excellent thermal stability, and high stiffness. Vulnerable to solvents.
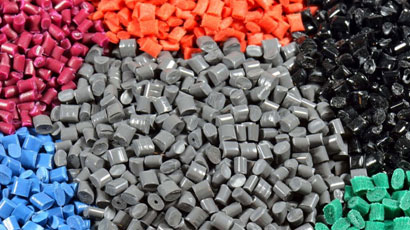
POM
Easy to machine. POM is an engineering thermoplastic used in precision parts requiring high stiffness, low friction, and excellent dimensional stability.
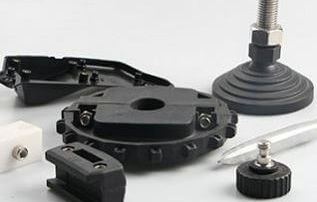
PMMA
UV resistant plastic with good abrasion resistance, stiffness and hardness.
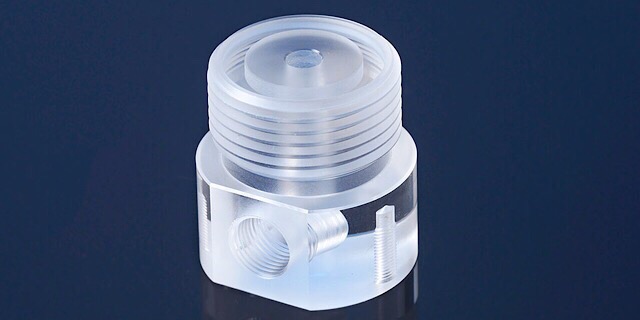
Standard Tolerances
If you do not provide us with your tolerances for Injection Moulding, we use standard tolerances DIN-16901. Tolerances can be greatly affected by part geometry and type of material. Our design engineers will consult you on every part of the project and will try to provide you with the highest degree of precision possible.
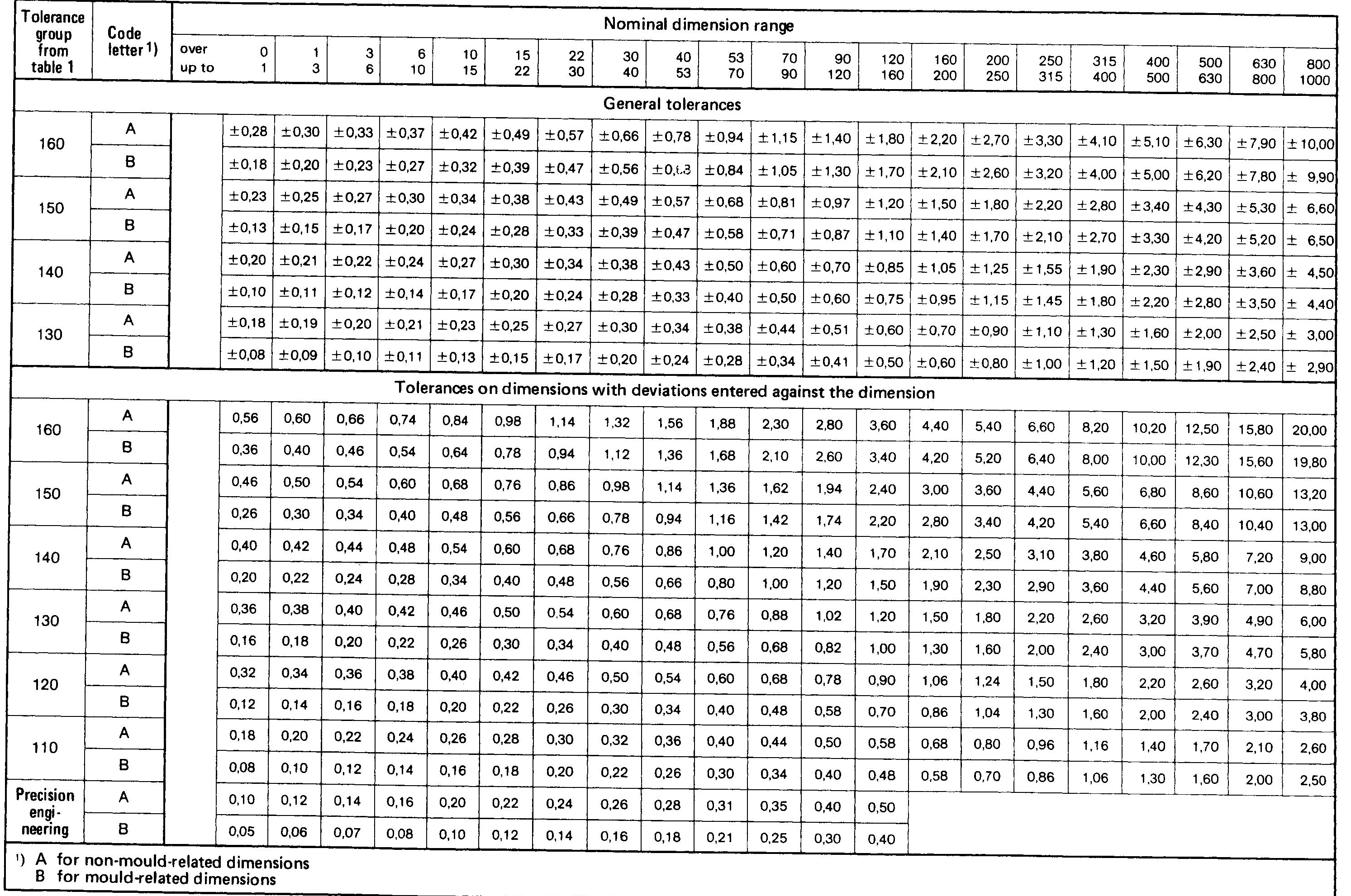
Finishes
Renderfact provides surface finishes on all Injection Moulded parts, including Gloss Finish, Semi-Glossy Finish, Matte and textured finishes.
A grade finishes are made using a diamond buffing process and yield shiny and glossy surfaces.
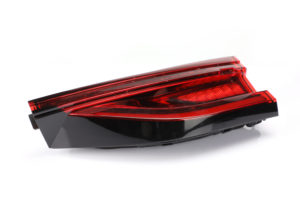
B grade finishes use grit sandpaper to produce parts with a slightly rougher finish than grade A parts. Products that undergo B grade finishing have a matte surface texture.
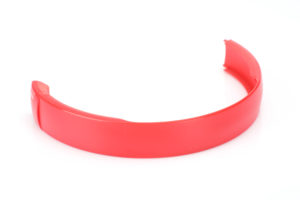
C grade finishes use grit sanding stones to produce a rough, uneven surface. Products that undergo C grade finishing have a matte surface texture.
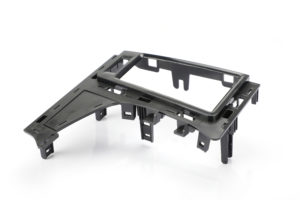
D grade finishes use grit and dry glass beads or oxide to produce a very rough textured finish. Depending on the type of material used, products can have a satin or dull finish.
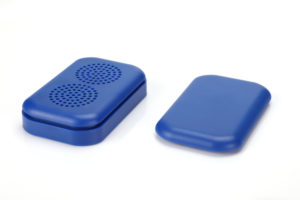
Applications
Rapid Tooling
Rapid tooling at Renderfact, you get to use the actual production grades of material, allowing you a much clearer picture of how the parts will act in real-world applications and enabling you to test and confirm you have made the correct material choices.
Rapid Prototyping
Rapid prototyping allows you to leverage the many advantages of computerized equipment to produce fast-turnaround prototypes, engineering models and high-quality end-use parts in the least possible time. Get in touch for your next rapid prototyping project.
End-Use Production
Renderfact is your ideal source for end use parts. Proven manufacturing processes like CNC Machining, and Injection Molding are complemented by our additive manufacturing capabilities like SLA, SLS, FDM, and DMLS, which provide you with incredible design freedom where complexity and small design iterations are not a roadblock.
Gallery
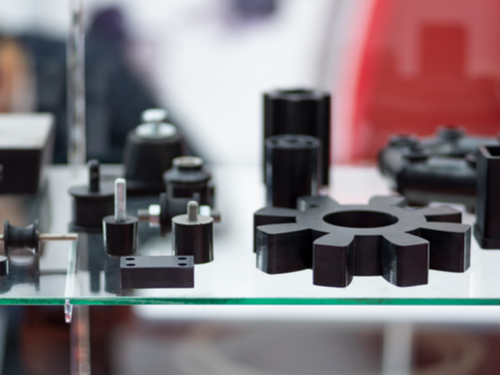
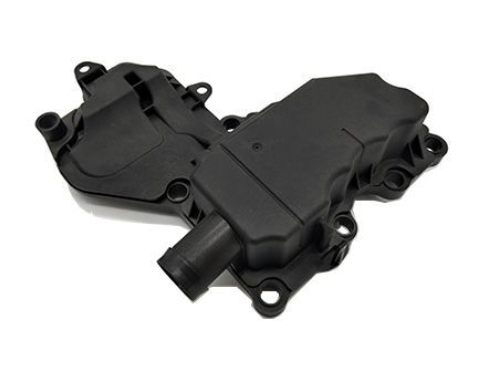
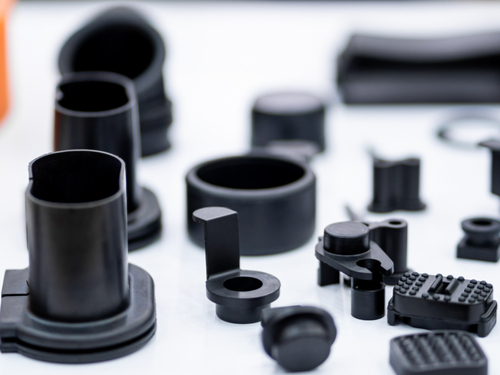
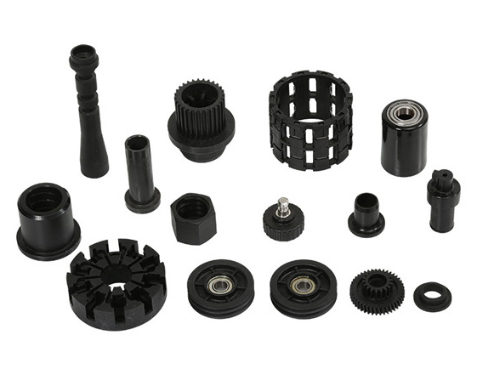
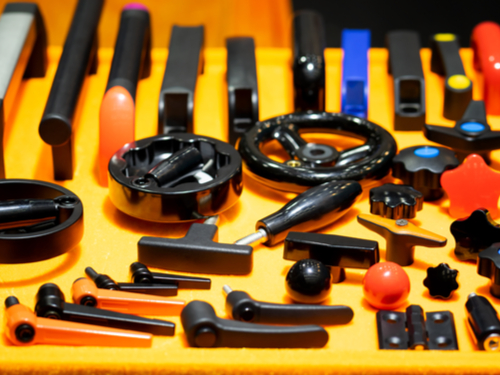
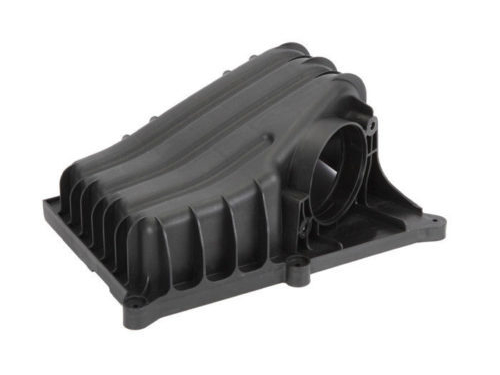
Quality Reports & Certifications
Full dimensional report
A Full work-up of dimensions can be provided for the parts you order for your peace of mind, on request.
Material certification
We have partnered with specialized Metallurgy Labs that provide and process special material certifications when requested.
First part verification
We provide first part verification services for a mutually agreed MOQ or on specific requests. We normally ship two sets of parts to the customer for verification and only once the parts have been validated, we move into full production.
Only 4 simple steps to complete your project. Follow the instruction and give it a try!