3D Printing Service
Machined prototypes and production parts delivered on time
CERTIFICATIONS
Renderfact 3-D Printing
Renderfact offers the latest technologies and comprehensive services of 3D printing including selective laser sintering, fused deposition modeling, stereolithography, direct metal laser sintering, polyjet, and HP Multi Jet Fusion ensuring high-quality printed parts with a wide range of 3D printing materials. 3D printing is a revolutionary technology that produces impossible-to-make parts directly from CAD file. 3D printing or additive manufacturing is a process of creating a three-dimensional object by adding material layer by layer until the object is complete. The main advantage of using 3D printing is its versatility and flexibility, which makes it suitable for rapid prototyping and low volume production to meet immediate needs for a variety of applications and industries including aerospace, automotive, consumer products, industrial products like special machinery, healthcare and medical, and architecture and construction industries.
At Renderfact we can built the appropriate 3D printing solution for our customer. We are your one-stop-shop for accurate, precise custom 3D printed parts at an affordable price.
Below are some of the benefits of 3D Printing and How it Works!
Advantages of 3d-printing
Accelerated Time-to-Market.
Production efficiency
Complexity geometry
Variety is free
Few constraints
Less waste
Metal 3D Printing (DMLS)
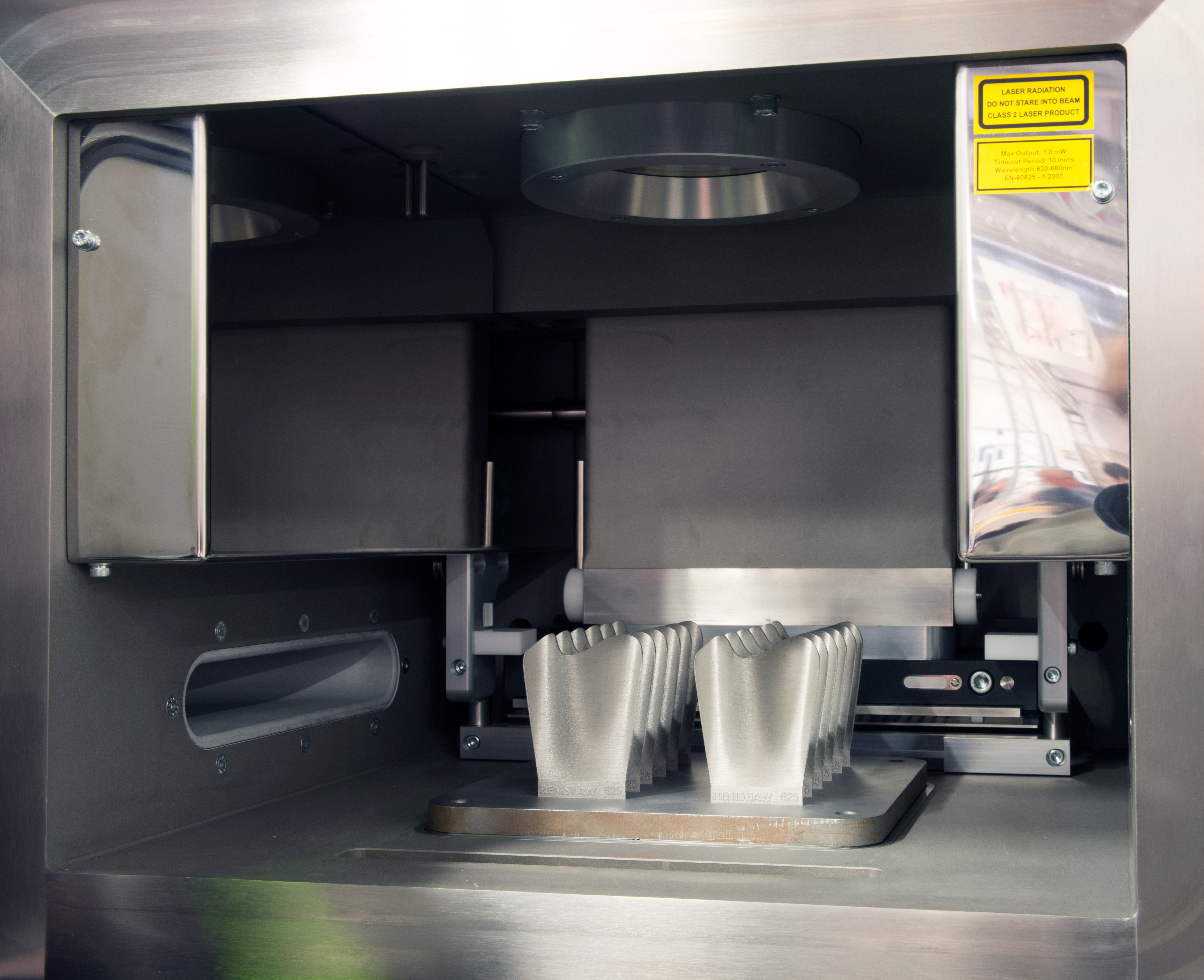
Metal 3D printing is a revolutionary technology that produces impossible-to-make parts directly from your CAD data. The DMLS machine begins sintering each layer—first the support structures to the base plate, then the part itself—with a laser aimed onto a bed of metallic powder. The combination of a fine-tuned laser, powder and advanced additive processes form a powerful design freedom. Direct Metal Laser Sintering (DMLS) fuses powdered metal and alloy materials to produce metal parts. DMLS produces fully realized metal parts, including tools and end-use parts for a variety of industries.
Advantages to this process include the ability to Produce complex geometries ideal for prototypes, low-volume parts, and end-use parts without the need for traditional manufacturing processes such as machining and casting. Parts can be made quickly with a minimum of material waste making them ideal for next-generation engineering in aerospace, medical, automotive and other industries.
Fused Deposition Modeling (FDM)
Fused Deposition Modeling (FDM) systems and related technologies are the most accessible and widely used form of 3D printing. FDM is a 3D printing process that extrudes melted plastic filament through a nozzle to create the part layer by layer. This process creates an accurate representation of the 3D file in relatively little time. The printed prototypes are rigid, especially compared to Selective Laser Sintering (SLS), which makes them a great fit for projects with a rigidity requirement. The production-grade thermoplastic material used is suitable for detailed functional prototypes, durable manufacturing tools & low-volume manufacturing parts.
FDM 3D printing technology builds durable and functional prototypes that can withstand rigorous testing. Ideal for functional parts, including prototypes, low-volume production, manufacturing aids, jigs and fixtures. The FDM process uses the same types of raw materials used in the injection molding process. This technology includes use of support material to create complex parts and assemblies.
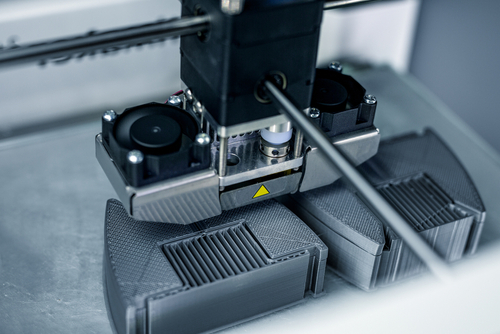
Selective Laser Sintering (SLS)
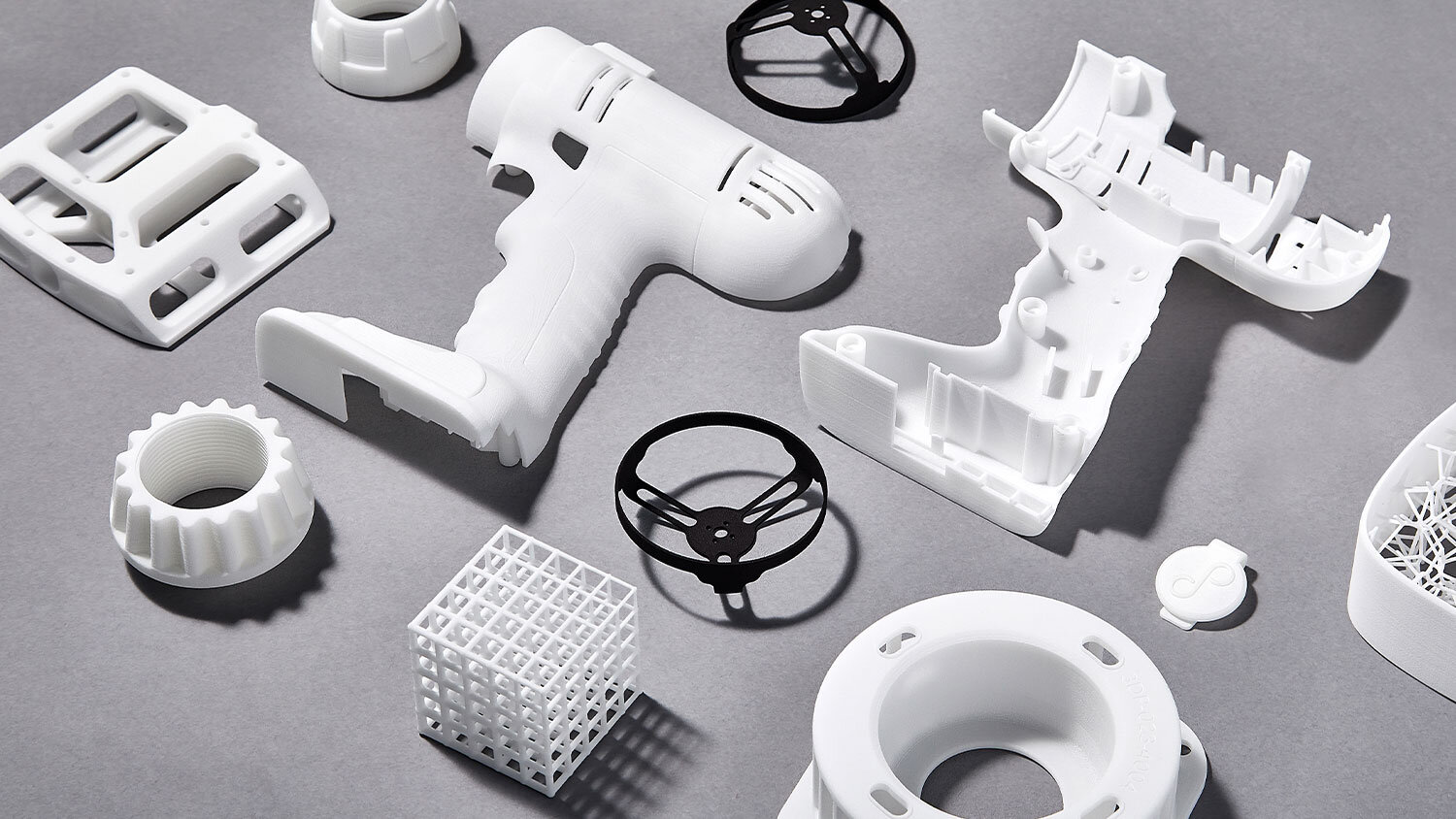
Selective Laser Sintering (SLS) is an Additive Manufacturing process that belongs to the Powder Bed Fusion family. In SLS, a laser selectively sinters the particles of a polymer powder, fusing them together and building a part layer-by-layer. The materials used in SLS are thermoplastic polymers that come in a granular form. SLS technology that produces highly accurate and durable parts that are capable of being used directly in end-use, low-volume production, or for rapid prototyping.
SLS is one of the most inexpensive options for industrial 3D printing services because it can build parts in bulk without support structure requirements. SLS offers a very high design freedom, high accuracy and produces parts with good and consistent mechanical properties, unlike FDM or SLA. SLS 3D printing has been used for consumer goods in the medical, footwear and beauty industries, Jigs, Fixtures & Other Tooling, Snap Fits & Housing.
Polyjet
PolyJet 3D printing technology known for its customizable material properties that produces smooth, accurate parts, prototypes and tooling. it can produce thin walls and complex geometries using the widest range of materials available with any technology. PolyJet 3D printing is like inkjet document printing. But instead of jetting drops of ink onto paper, PolyJet 3D printers jet layers of liquid photopolymer onto a build tray and cure them with UV light. The layers build up one at a time to create a 3D model or prototype. Fully cured models can be handled and used immediately, without additional post-curing.
Our advanced 3D printing equipment allows for fast product creation in complex shapes, intricate details and delicate features. The technology works with a vast array of materials, including rigid opaque in hundreds of vibrant colors, clear and tinted translucent shades, rubber-like flexible materials, and specialized photopolymers for 3D printing in the dental, medical and consumer product industries.
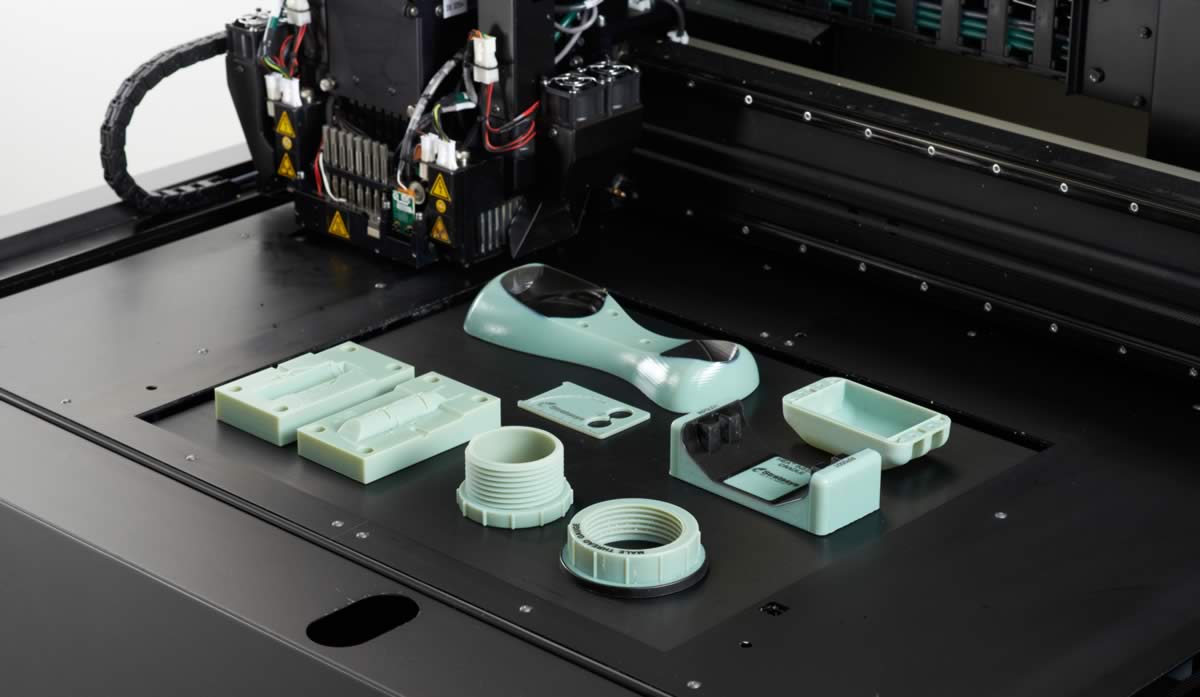
Stereolithography (SLA)
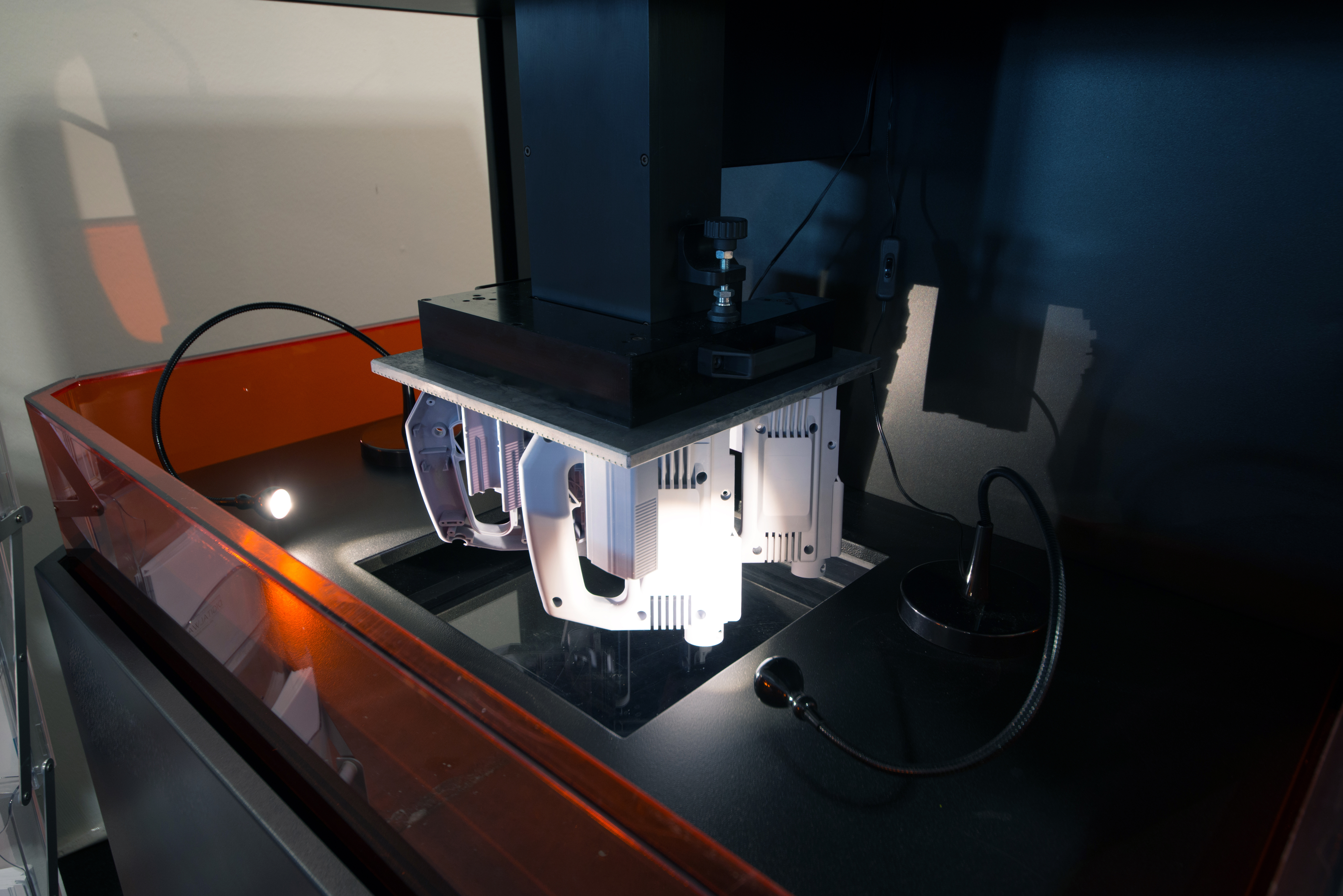
Stereolithography commonly known as resin 3D printing. SLA is one of the most accurate of the additive technologies, the Stereolithography 3D printing process is a popular choice amongst engineers looking for fine detailed, small, featured parts as well as extraordinarily large components. The SLA machine begins drawing the layers of the support structures, followed by the part itself, with an ultraviolet laser aimed onto the surface of a liquid thermoset resin. After a layer is imaged on the resin surface, the build platform shifts down and a recoating bar moves across the platform to apply the next layer of resin. The process is repeated layer by layer until the build is complete.
SLA is a go-to choose for 3D printed models that require accurate features and a smooth surface finish. Renderfact offers both standard and high-resolution options for fine detail parts and can also print larger sized parts and products. With the ability to produce complex features with good mechanical properties, SLA 3D prints are often used for final fit checks before moving to injection molding services.
Multi Jet Fusion (MJF)
Multi Jet Fusion is a new 3D printing technology, offering you more possibilities for complex, lower-cost parts. Whether used in serial production for single parts or batch manufacturing by shipsets of multiple part numbers, Multi Jet Fusion offers a faster, more cost-effective process for 3D printed parts. The Multi Jet Fusion process starts with a layer of material applied to the work area. In the opposite direction, in one continuous pass, the machine prints fusing and detailing agents across the full working area. This pass combines the printing with the fusing energy, and the process is completed. The innovative technology prints quickly along the bed width, enabling extreme precision and dimensional accuracy.
Multi Jet Fusion is an excellent technology for applications like thin walls, ductwork, connectors, brackets, housings clips and guides. Industries can benefit from Multi Jet Fusion higher volume capabilities through limited run, pre-production and spare parts.

Materials
3D-Printing can be done both on plastics as well as metals. Metals include stainless steel and aluminum, and plastics include Nylon, PLA, Resin, ABS, PETG, TPU, ASA, PEI
Aluminum
Aluminum is a highly ductile metal, making it easy to machine. The material has a good strength-to-weight ratio and is available in many types for a range of applications.
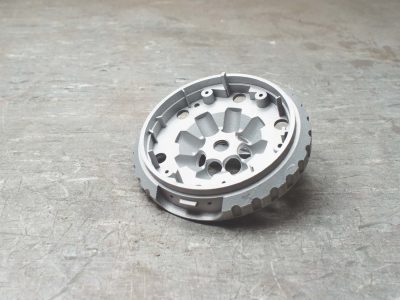
Stainless steel
High tensile strength, corrosion and temperature resistant. Stainless steel alloys have high strength, ductility, wear and corrosion resistance. They can be easily welded, machined and polished.
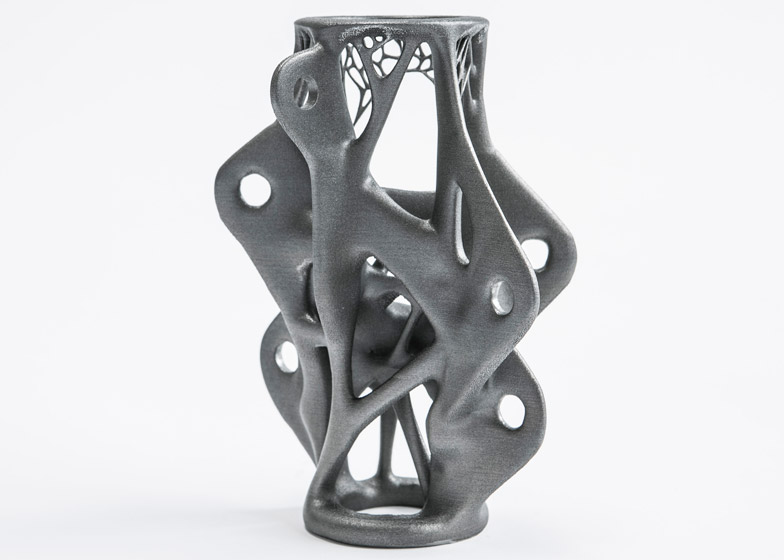
Nylon
Used to substitute functional injection moulded parts, good chemical resistance.
- SLS Nylon Materials
- MJF Nylon Materials
- FDM Nylon Materials
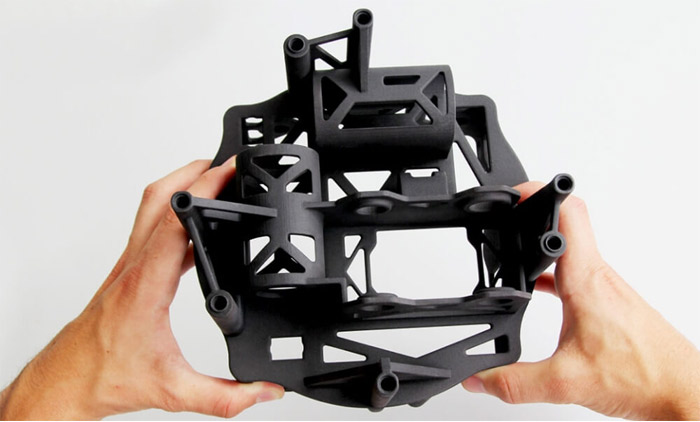
PLA
High stiffness, good detail, affordable.
- FDM PLA Materials
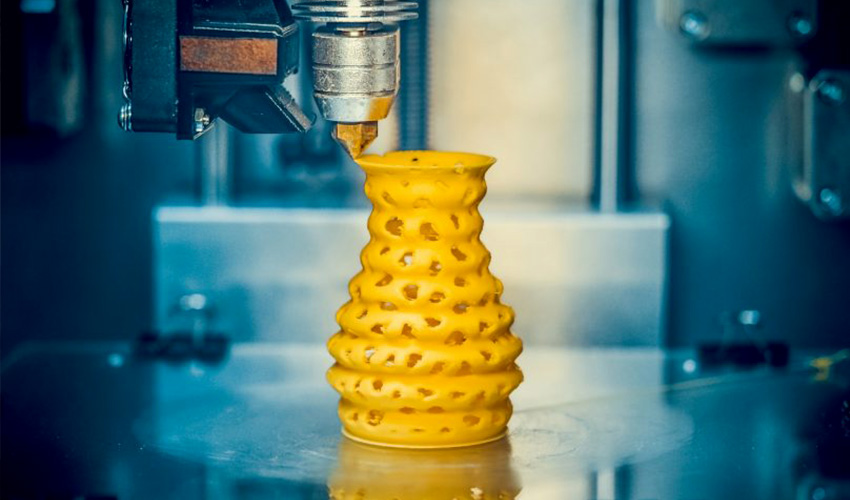
Resin
High detail and smooth surface, injection mold-like prototyping.
- SLA Resin Materials
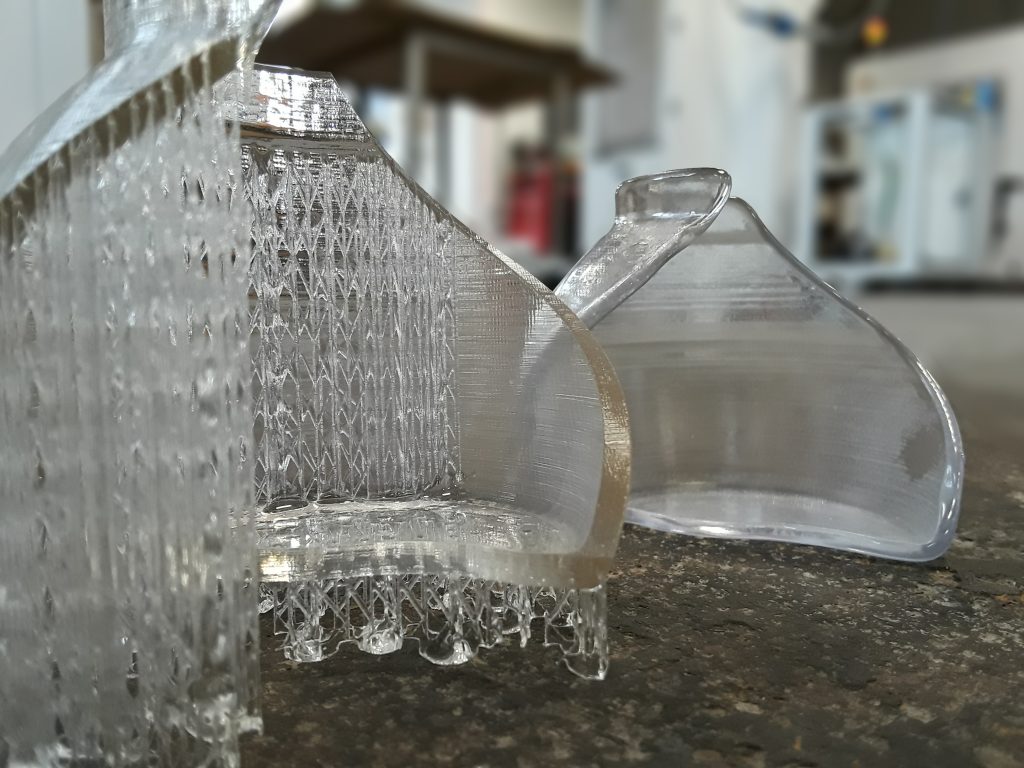
ABS
Commodity plastic, improved mechanical and thermal properties compared to PLA.
- FDM ABS Materials
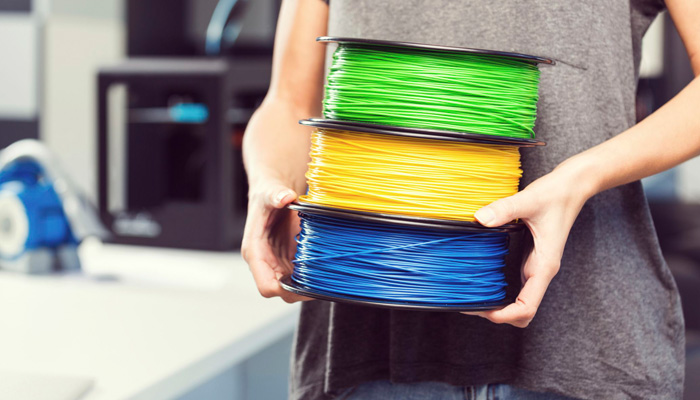
PETG
Good for mechanical parts with high impact resistance and flexibility. Sterilizable.
- FDM PETG Materials
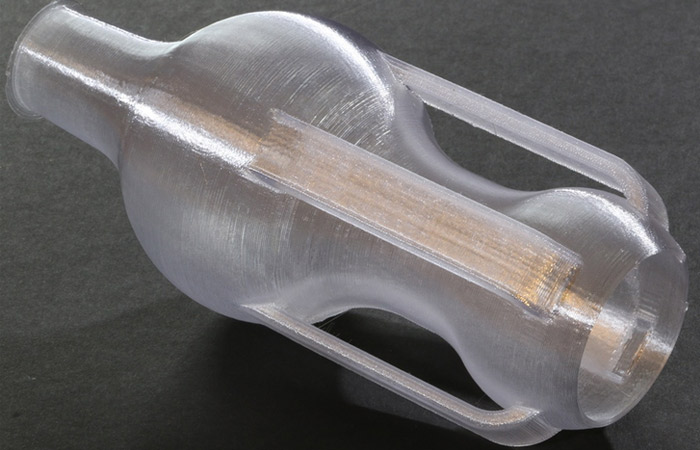
TPU
Rubber-like material, suitable for tubes, grips, seals and gaskets.
- FDM TPU Materials
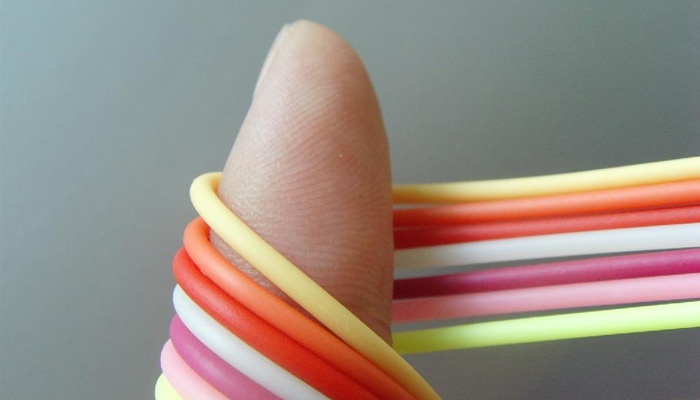
ASA
UV stability and high chemical resistance, preferred material for outdoor applications.
- FDM ASA Materials
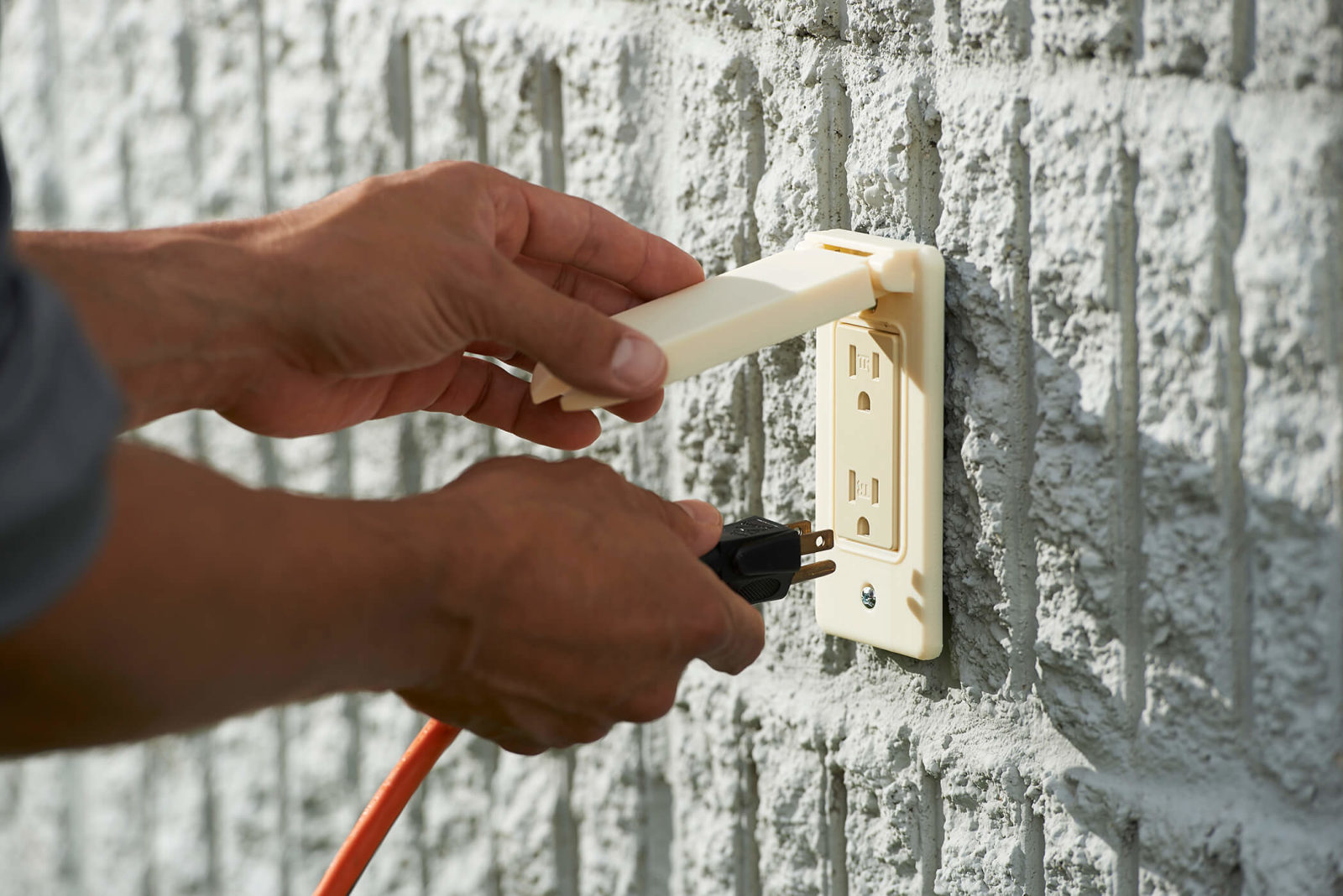
PEI
Engineering plastic, high performance applications, flame retardant.
- FDM PEI Materials
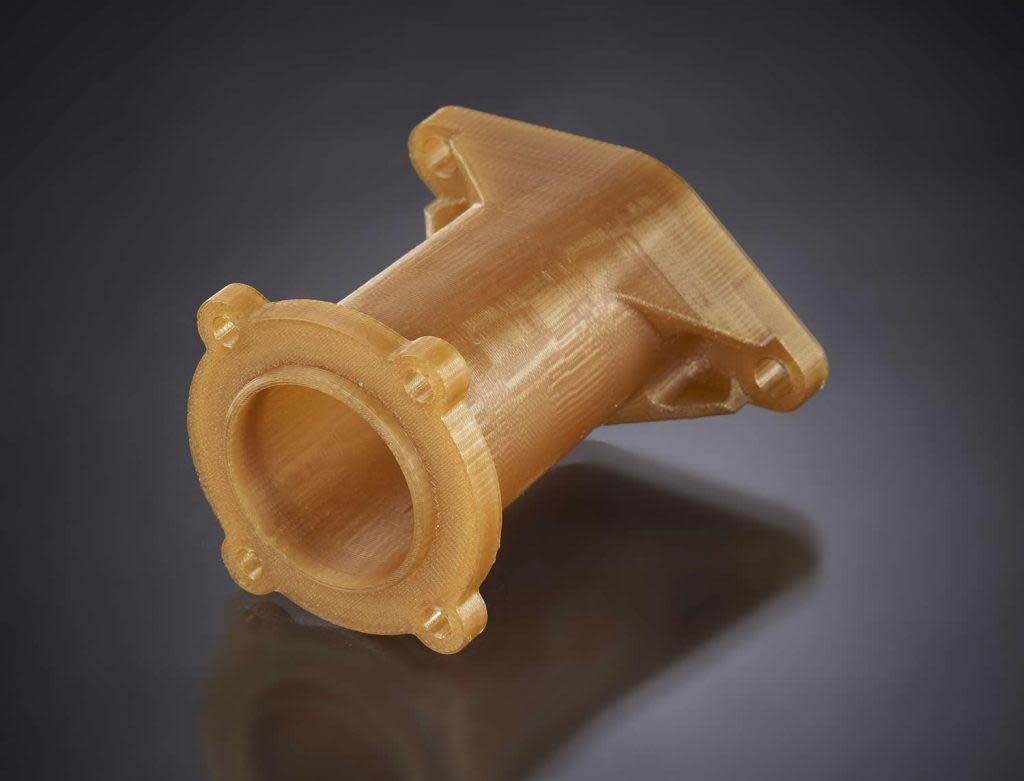
PC
Industrial thermoplastic with high accuracy, durability and high strength.
- FDM PC Materials
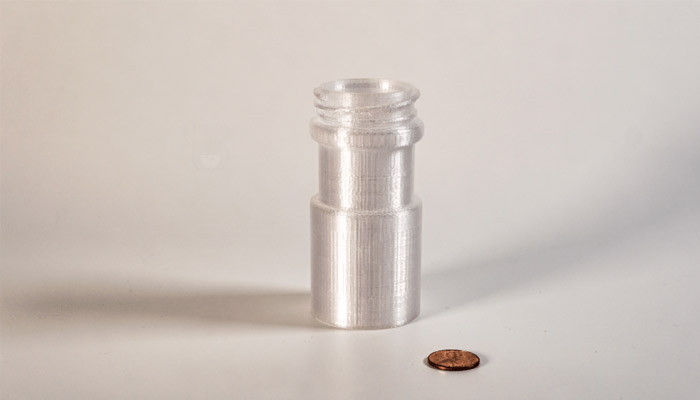
Standard Tolerances
If you do not provide us with your tolerances for 3D-Printing , we use standard tolerances for all processes as mentioned below. Tolerances can be greatly affected by part geometry and type of material. Our Engineers will consult you on every part of the project and will try to provide you with the highest degree of precision possible.
Service | Standard Tolerances |
---|---|
FDM | Industrial FDM printing has a dimensional tolerance of ± 0.15% and a lower limit of ± 0.2 mm. |
SLA | Industrial SLA printing has a dimensional tolerance of ± 0.15% and a lower limit of ± 0.01 mm. |
SLS | SLS printing has a dimensional tolerance of ± 0.3% and a lower limit of ± 0.3 mm. |
Metal 3D Printing | Metal printing has a dimensional tolerance of ± 0.1 mm. |
Material Jetting | Material jetting has a dimensional tolerance of ± 0.1% and a lower limit of ± 0.05 mm. |
Finishes
Renderfact provides surface finishes on all 3D-printed parts, including painting, polishing, powder coating and bead blasting.
Painting the surface of a part improves its aesthetic appearance and can provide brand recognition to consumers. In addition, painting can have a protective effect on parts.
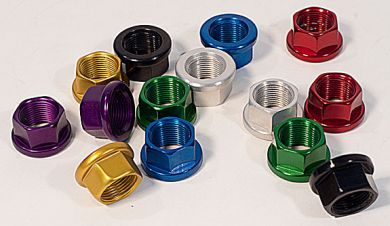
Polishing is the process of creating a smooth and shiny surface, either through physical rubbing of the part or by chemical interference. The process produces a surface with significant specular reflection, but in some materials is able to reduce diffuse reflection.
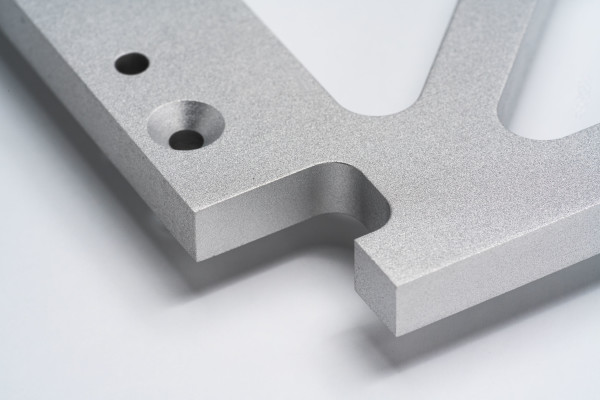
Powder coating forms a durable, wear resistant and corrosion resistant layer on the surface of parts. Powder coating can be used to apply colors to parts and is compatible with any metal.
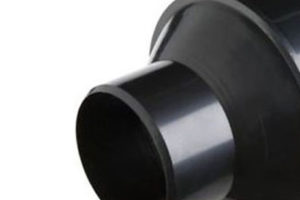
Bead blasting results in parts with a smooth surface with a matte texture. Used mainly for visual applications and can be followed by other surface treatments.
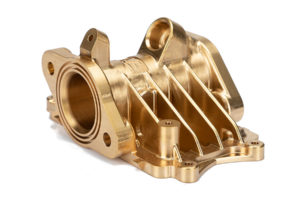
Applications
Rapid Tooling
Rapid tooling at Renderfact, you get to use the actual production grades of material, allowing you a much clearer picture of how the parts will act in real-world applications and enabling you to test and confirm you have made the correct material choices.
Rapid Prototyping
Rapid prototyping allows you to leverage the many advantages of computerized equipment to produce fast-turnaround prototypes, engineering models and high-quality end-use parts in the least possible time. Get in touch for your next rapid prototyping project.
End-Use Production
Renderfact is your ideal source for end use parts. Proven manufacturing processes like CNC Machining, and Injection Molding are complemented by our additive manufacturing capabilities like SLA, SLS, FDM, and DMLS, which provide you with incredible design freedom where complexity and small design iterations are not a roadblock.
Gallery
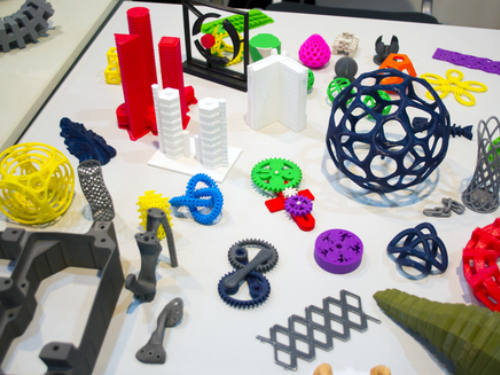
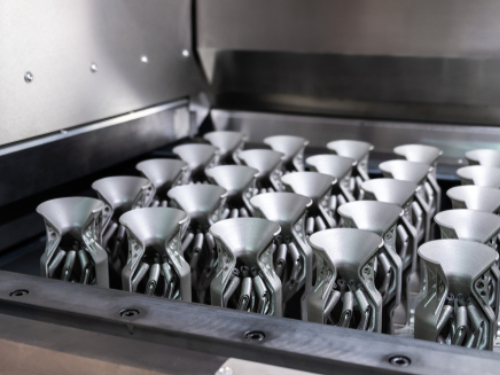
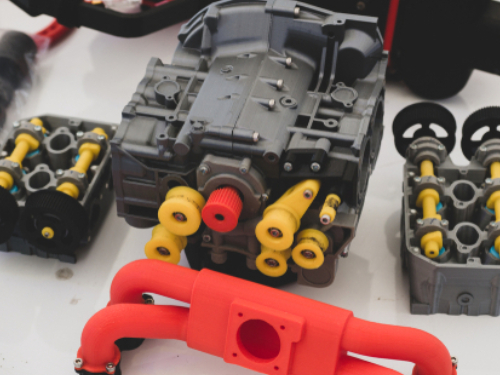
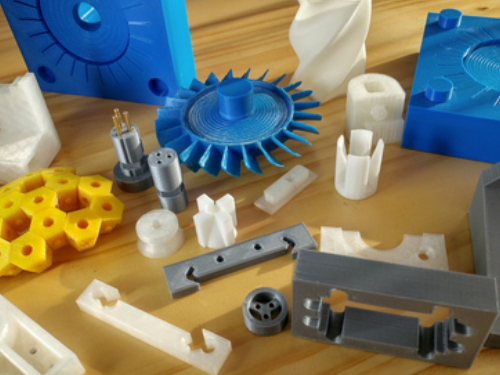
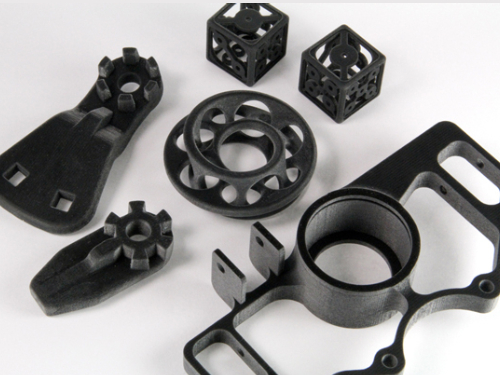
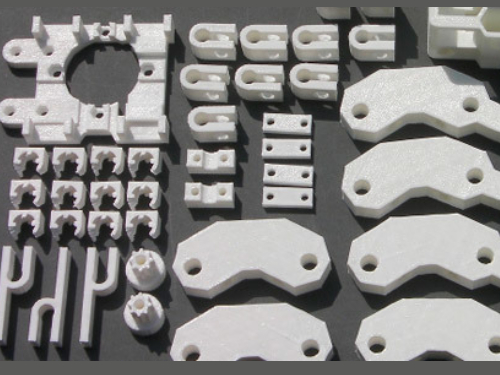
Quality Reports & Certifications
Full dimensional report
A Full work-up of dimensions can be provided for the parts you order for your peace of mind, on request.
Material certification
We have partnered with specialized Metallurgy Labs that provide and process special material certifications when requested.
First part verification
We provide first part verification services for a mutually agreed MOQ or on specific requests. We normally ship two sets of parts to the customer for verification and only once the parts have been validated, we move into full production.
Only 4 simple steps to complete your project. Follow the instruction and give it a try!