EDM Machining Service
Machined prototypes and production parts delivered on time
CERTIFICATIONS
RenderFact EDM Machining
At Renderfact, we use advanced equipment to offer you a variety of EDM machining services including EDM Wire-cut, EDM Sinker and EDM Drilling. Electrical Discharge Machining (EDM) is the process of cutting metal to precise shapes using electricity. EDM machining (electrical discharge machining also known as spark machining) is one of the most accurate manufacturing processes available for creating complex shapes and geometries within parts and assemblies. The absence of heavy force facilitates adherence to tight, repeatable tolerances and results in remarkable consistency. It is also easy to produce highly complex or contoured shapes with wire EDM machining, providing greater flexibility to designers.
Renderfact brings together years of EDM expertise with advanced sinker, EDM Drill and wire style EDM machines that utilize the latest computer systems. Our EDM Machine Shop allows us to manufacture parts that cannot be drilled, tapped, or milled in small, detailed and hard-to- reach areas.
Below are some of the benefits of EDM Machining and How it Works!
Advantages of EDM Machining
Superior Consistency
Simultaneous Cutting
Eliminates Finishing
No physical contact with the machine part
Extremely precise
Highly repeatable
EDM Drill
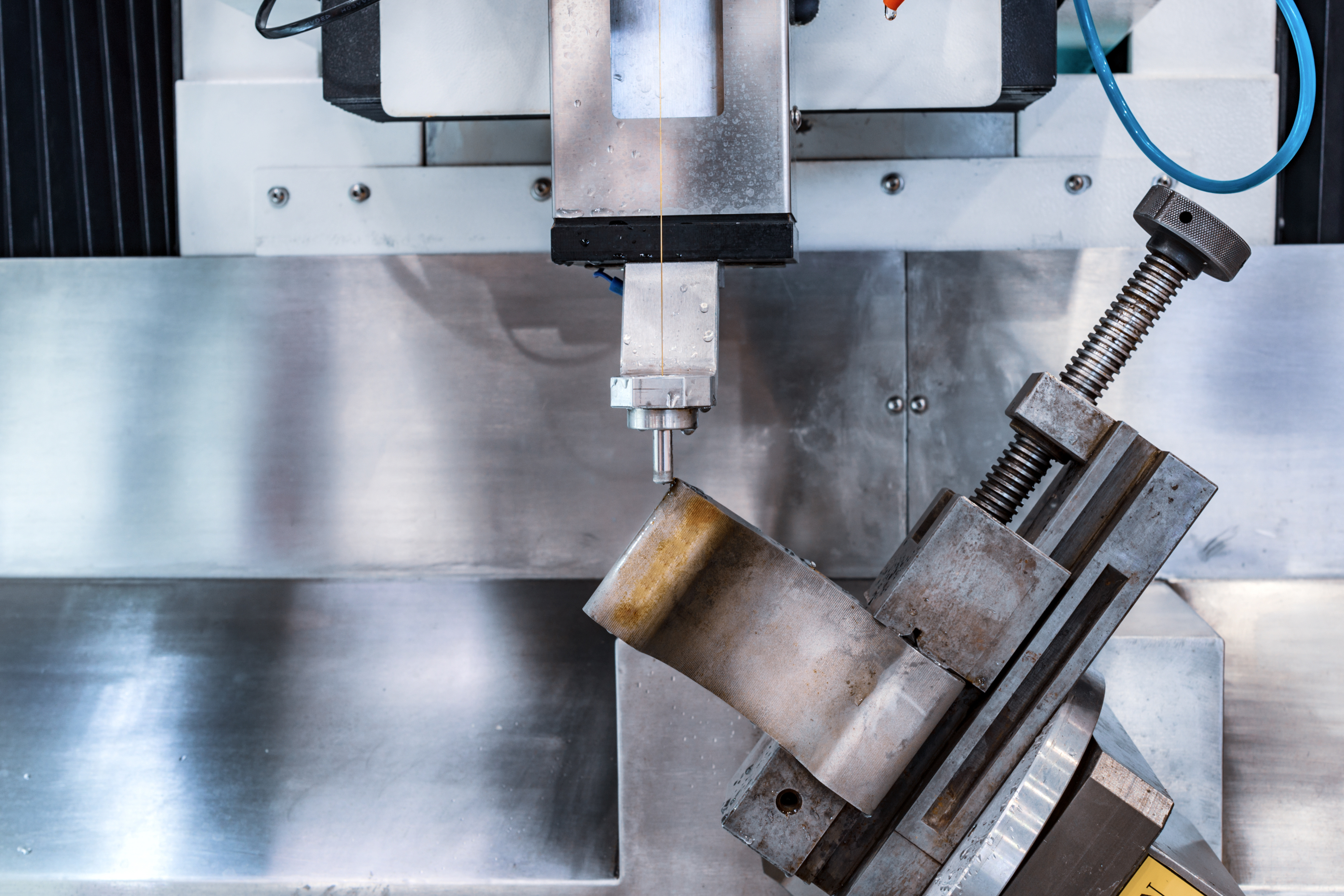
Small hole EDM drilling is ideal for creating injection nozzles in molds and coolant holes in tooling, as well as start holes for wire EDM operations. Since both processes are types of electrical discharge machining (EDM), it is often more economical to use this combination for hardened materials.
Hole drilling EDM uses low-cost electrode tube (normally brass or copper material) to drill holes on an electrically conductive material at a very high speed, the hole depth diameter ratio can reach up to 200. The hole diameter is normally from 0.3mm to 3.0mm, with five axis configuration the machine can drill hole at any angles on an inclined surface. This technology is widely used for drilling holes in aerospace, energy, cutting tools, automotive, medical, mold and die industries.
Start hole EDM is a specifically quick and efficient metalworking method, which can be applied to process very thin as well as very thick materials., our start hole EDM, electric spark erosion can be used to machine the smallest holes by electrodes quickly, smoothly, free from burrs, and precisely into almost any conductive material.
EDM Wirecut
EDM Wire-cut also known as Wire burning or cutting, Wire Electrical Discharge Machining uses a thin wire electrode (0.005″–0.010″ in diameter) made from brass or copper to cut conductive material along a pre-programmed path. Wire EDM machines use a thin wire that produces a recurring electrical discharge between the wire and the workpiece to cut into the work material, which is flushed and cooled with deionized water. Since the wire never touches the metal, the process produces a clean surface finish that does not require deburring, making it ideal for applications involving intricate designs.
Renderfact takes pride in the ability to take on any job regardless of the complexity. Through our state-of-the-art EDM department, we manufacture parts that would not be possible with conventional machining Using a strand of wire as a cutting tool creates a linear line, and therefore Wire EDM services are commonly used to cut all the way through the material. Wire EDM is best suited for projects that have intricate tolerances and material stress limitations.
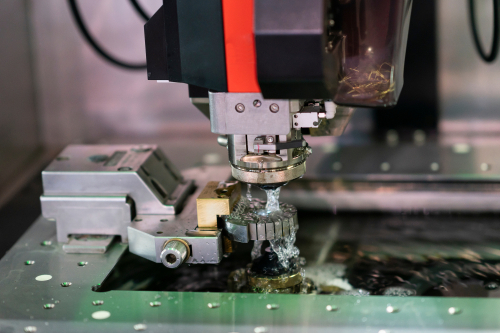
EDM Sinker
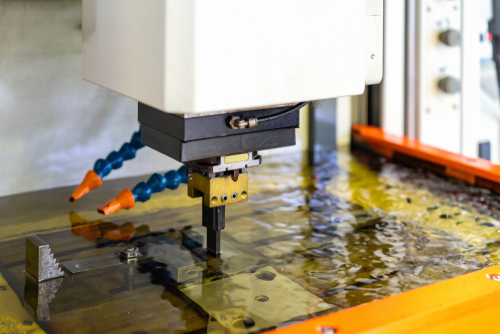
A sinker EDM has many uses from making starting holes for wire EDM to mirroring an electrode shape into the desired shape in the part. Sinker EDM machines use an electrode and workpiece submerged in liquids such as oil or dielectric water.Power supply is connected to the electrode and generates electrical potential between both parts, producing a breakdown to form a plasma channel and spark jumps. The sparks initiated by the power supply often strike one after another. As the sparks continue to form, the base metal begins to erode and the electrode is lowered, causing the “ramming” or “sinking” effect of this EDM machine. When the process is complete and every part has been removed, the base metal has been eroded in a very specific shape or design – like an engraving. EDM machines allow for quicker manipulations of hard metals giving companies the best efficiency available today for industrial productions.
EDM sinker burns any electrically conductive material, whether soft or hard, without inducing stresses into the material. Die-sinker EDMs often can solve the problems posed by machining materials such as high-nickel-content alloys used in the aerospace industry. Also, the complicated shapes and deep pockets commonly found in the mold making industry are two-part features that pose a challenge to CNC chipping machines. However, these geometries lend themselves well to the CNC die-sinking process.
Materials
EDM Machining works on metals such as aluminum, brass, copper, tool steel and other materials like titanium, tungsten, carbide, molybdenum and other exotic metals.
Aluminum
Aluminum is a highly ductile metal, making it easy to machine. The material has a good strength-to-weight ratio and is available in many types for a range of applications.
- Aluminum 6061
- Aluminum 6061-T651
- Aluminum 6063
- Aluminum 7075
- Aluminum 6082
- Aluminum 2024
- Aluminum 5052
- Aluminum 5083
- Aluminum ADC12 (A380)
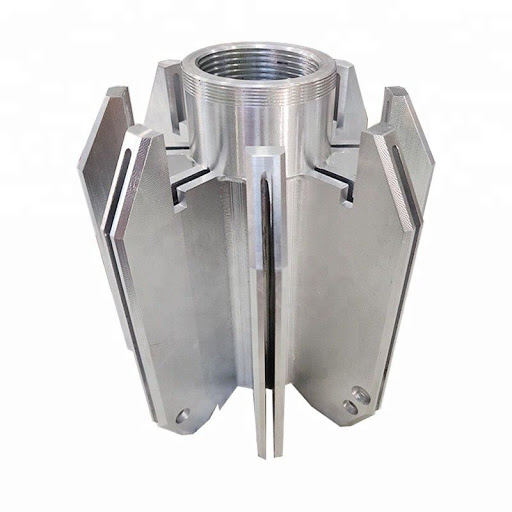
Copper
Copper displays excellent thermal conductivity, electrical conductivity and plasticity. It is also highly ductile, corrosion resistant and can be easily welded.
- Copper
- Copper 101
- Copper for EDM
- Beryllium copper
- Chromium zirconium copper
- Tungsten copper
- Antimony copper
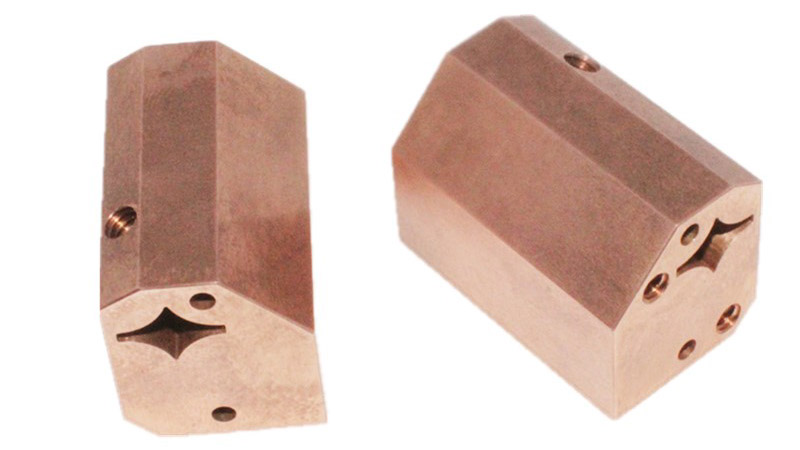
Brass / Bronze
Brass has desirable properties for a number of applications. It is low friction, has excellent electrical conductivity and has a golden (brass) appearance.
- Brass 2680
- Brass H59
- Brass H62
- Brass 260
- Brass 385
- Brass CAD260
- Brass 360
- Tin phosphor bronze
- Aluminum bronze plate
- Tin bronze
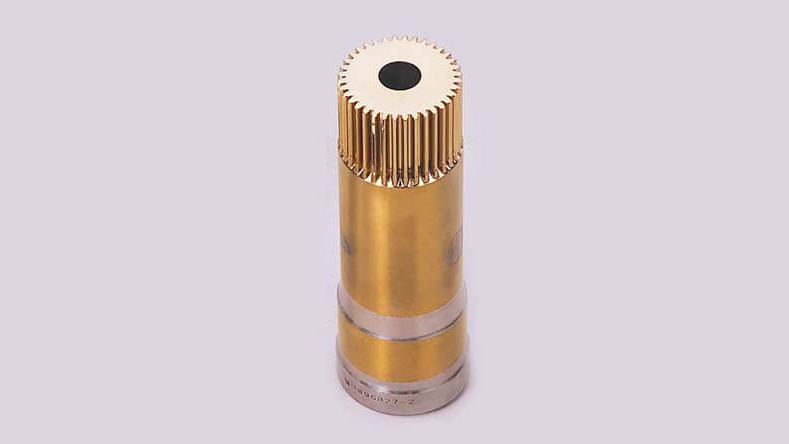
Tool Steel
Tool steels are a family carbon and alloy steels having distinct characteristics such as hardness, wear resistance, toughness, and resistance to softening at elevated temperatures
- A-2, A-5, A-6, A-8
- D-2, D-3, D-5
- DC-53
- H-11, H-12, H-13, H-19
- L-6
- M-1, M-2, M-3, M-4, M-2
- O-1, O-6
- S-1, S-7
- T-1
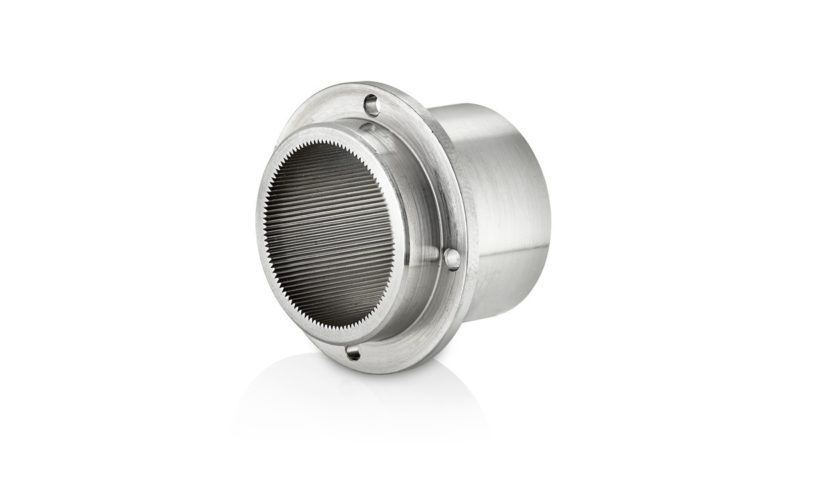
Other Metals
- Titanium
- Tungsten
- Carbide
- Exotic Metals
- Molybdenum
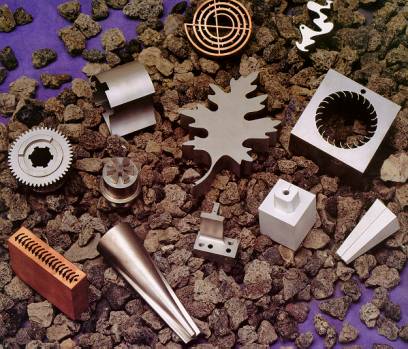
Titanium
- TC4 Titannium Alloy
- TC5 Titanium Alloy
- Military-grade titanium Alloy
- Food-grade titanium Alloy
- R53400 Titanium Alloy 9
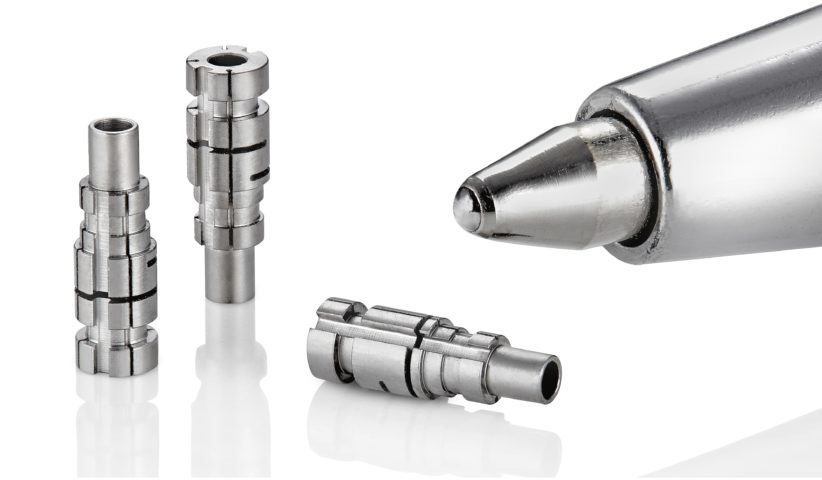
Plastics
- ABS
- PC
- ABS+PC
- PMMA
- POM
- PP
- PA
- PEEK
- PET
- PVC
- PPSU
- PPS
- PTFE
- PBT
- PE
- PEI
- HDPE
- UPE
- CPVC
- EPP
- FR-4
- HIPS
- LDPE
- PAI
- PETG
- PPA
- PS
- PVDF
- Bakelite

Standard Tolerances
If you do not provide us with your tolerances for EDM Machining , we use standard tolerances for all processes as mentioned below. Tolerances can be greatly affected by part geometry and type of material. Our Engineers will consult you on every part of the project and will try to provide you with the highest degree of precision possible.
Service | Standard Tolerances |
---|---|
EDM Drill | 0.0010″ to 0.0005″ and high precision tolerances as tight as 2µm Surface finishes down to 4Ra µin (micro inch) |
EDM Wirecut | EDM Drilling: +/- 0.001” TOLERANCE |
EDM Sinker | EDM Sinker: +/- 0.0002” TOLERANCE |
*(Typical tolerance, but can vary due to type of material) |
Finishes
Renderfact provides surface finishes on all EDM parts, including anodizing, electroplating, bead blasting, polishing, brushing, powder coating, and painting.
Anodizing improves corrosion resistance, enhancing wear resistance and hardness, and protecting the metal surface. Widely used in mechanical parts, aircraft, and automobile parts, precision instruments, etc.
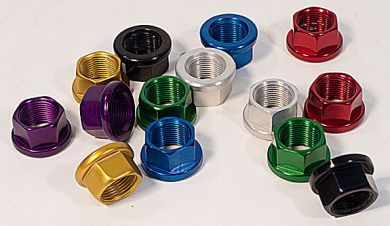
Bead blasting results in parts with a smooth surface with a matte texture. Used mainly for visual applications and can be followed by other surface treatments.
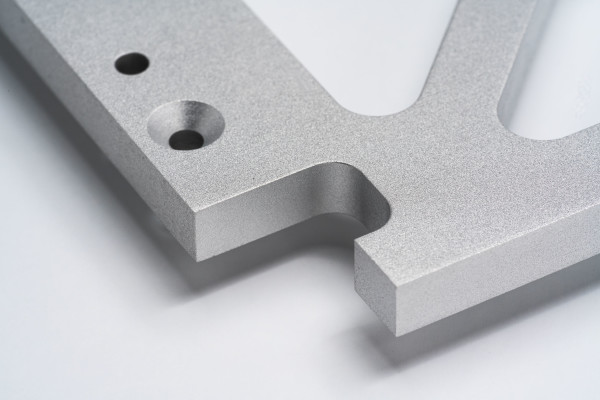
Powder coating forms a durable, wear resistant and corrosion resistant layer on the surface of parts. Powder coating can be used to apply colors to parts and is compatible with any metal.
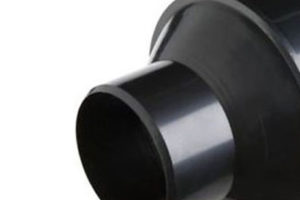
Electroplating can be functional, decorative or corrosion-related. Many industries use the process, including the automotive sector, in which chrome-plating of steel automobile parts is common.
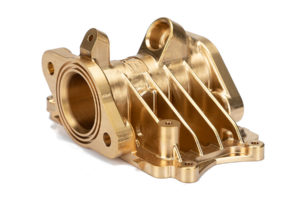
Polishing is the process of creating a smooth and shiny surface, either through physical rubbing of the part or by chemical interference. The process produces a surface with significant specular reflection, but in some materials is able to reduce diffuse reflection.
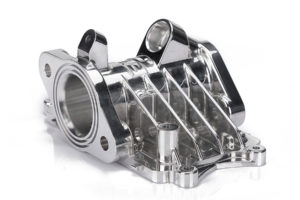
Brushing is a surface treatment process in which abrasive belts are used to draw traces on the surface of a material, usually for aesthetic purposes. Most commonly applied to aluminum.
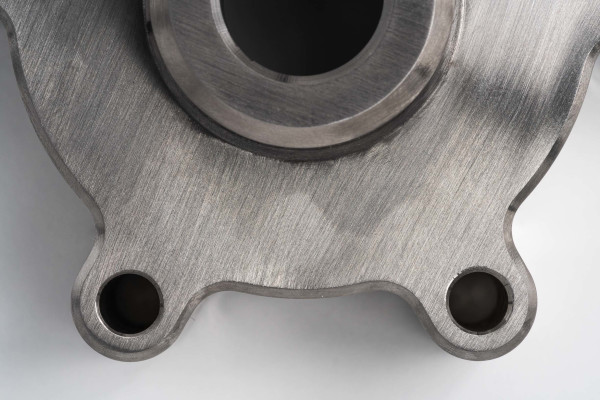
Painting the surface of a part improves its aesthetic appearance and can provide brand recognition to consumers. In addition, painting can have a protective effect on parts.
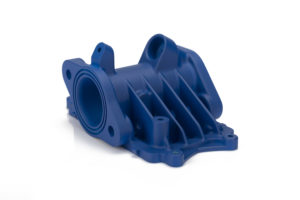
Applications
Rapid Tooling
Rapid tooling at Renderfact, you get to use the actual production grades of material, allowing you a much clearer picture of how the parts will act in real-world applications and enabling you to test and confirm you have made the correct material choices.
Rapid Prototyping
Rapid prototyping allows you to leverage the many advantages of computerized equipment to produce fast-turnaround prototypes, engineering models and high-quality end-use parts in the least possible time. Get in touch for your next rapid prototyping project.
End-Use Production
Renderfact is your ideal source for end use parts. Proven manufacturing processes like CNC Machining, and Injection Molding are complemented by our additive manufacturing capabilities like SLA, SLS, FDM, and DMLS, which provide you with incredible design freedom where complexity and small design iterations are not a roadblock.
Gallery
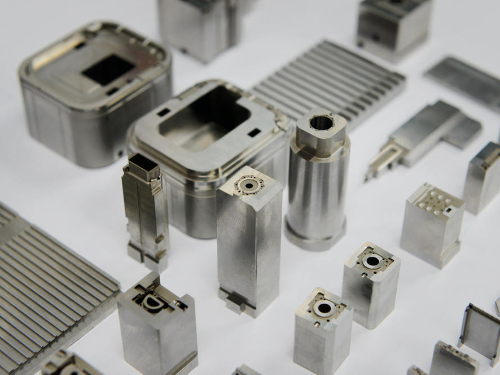
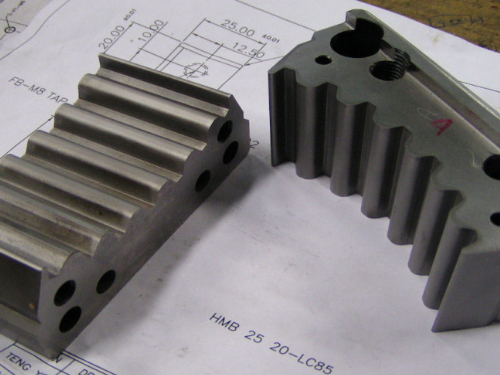
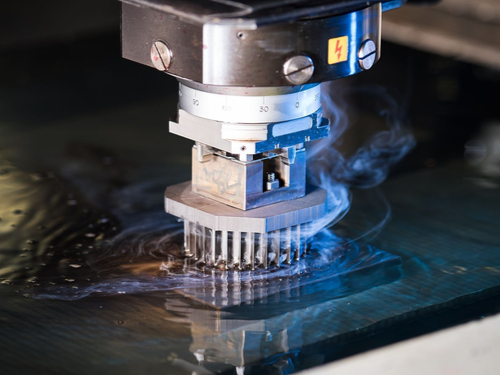
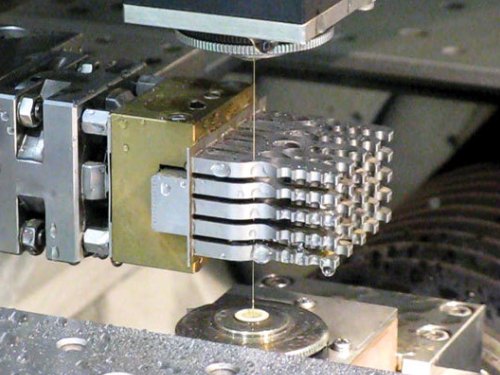
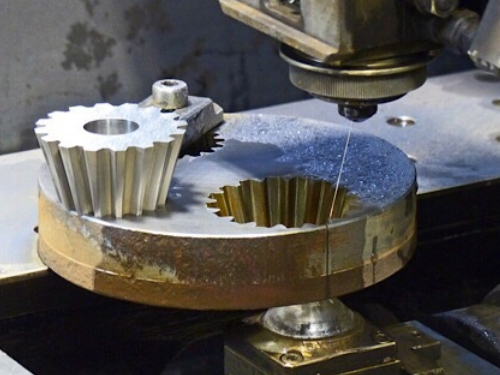
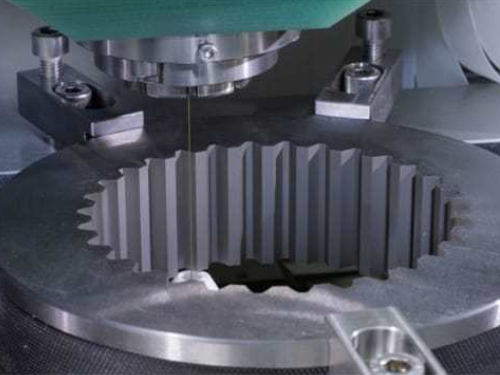
Quality Reports & Certifications
Full dimensional report
A Full work-up of dimensions can be provided for the parts you order for your peace of mind, on request.
Material certification
We have partnered with specialized Metallurgy Labs that provide and process special material certifications when requested.
First part verification
We provide first part verification services for a mutually agreed MOQ or on specific requests. We normally ship two sets of parts to the customer for verification and only once the parts have been validated, we move into full production.
Only 4 simple steps to complete your project. Follow the instruction and give it a try!