High Pressure Die Casting Service
Machined prototypes and production parts delivered on time
CERTIFICATIONS
RenderFact High Pressure Die Casting
High Pressure Diecasting’s (HPDCs) are light-weight alternative components made from forcing molten metals into a mold at high speed and pressure. Casting molten metals allows for once multi-piece, welded-together structures to now be singular, aluminum castings – performing the same task with less mass and variability. The process allows fast, precise, cost effective production of aluminum or zinc die castings, meeting the needs of hi-tech industries where product appearance and dimensional tolerances are critical.
Renderfact has a professional die-casting parts production line, focusing on aluminum alloy & zinc alloy die-casting services, and has become a technology-leading die-casting product manufacturer. It provides innovative metal die-casting technology for aerospace, auto parts, automobile wheels, electronic accessories, medical supplies, replica sculptures, household hardware, construction accessories, etc.
Advantages of High Pressure Die Casting
Rapid manufacturing
High-precision products
Suitable for finishing
Lightweight products
Better performance
Thin-walled products
HIGH PRESSURE DIE CASTING
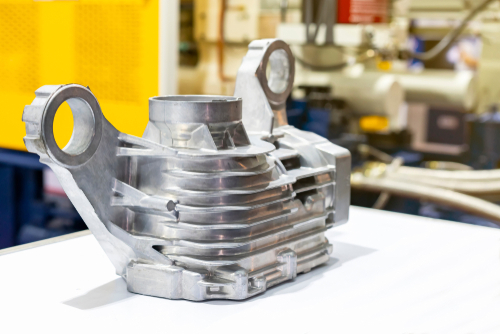
Die casting is a metal casting process that is characterized by forcing molten metal under high pressure into a mold cavity. Most die castings are made from non-ferrous metals, specifically zinc, copper, aluminum, magnesium, lead and tin-based alloys. Depending on the metal being used, the injection unit that fills the mold can either be hot chamber or cold chamber. In hot chamber die casting, the metal is held within the diecasting machine itself, then drawn into the chamber and forced into the mold by the injection piston. These parts of the machine are in constant contact with the molten metal. The molds—also known as tools or dies—are created using steel and are specially designed for each project. This allows each component to be created with accuracy and repeatability.
The versatility, quality stability and accuracy of the die casting process have been widely used in various industries. Commonly used aluminum alloy die-casting parts are automobile wheels, radiator equipment, electronic parts, power connectors, communication equipment, electrical enclosures, etc. Zinc alloy die-casting parts are often used in automotive circuit parts, controller components, household door handles, children’s toys, miniature models, etc. Magnesium alloy die-casting parts are commonly used in electronic equipment, medical equipment, power line connectors and laboratory equipment accessories.
Materials
High Pressure Die Casting can be done on metals such as Aluminum, Zinc and Magnesium Alloys.
Aluminum alloy
– Aluminum is a highly ductile metal, making it easy to machine. The material has a good strength-to-weight ratio and is available in many types for a range of applications.
- ADC12/ ALSI 132
- ADC 6
- ADC10
- A360
- A380
- A356
- A413
- LM 2
- LM 4
- LM 6
- LM 9 / ALSI 10MG
- LM 13
- LM 16
- LM 24
- LM 25
- ADC 12 SR. MOD.
- HYPER / GDC 12
- AC4CH
- LEG 231 / DLM20
- B390
- K-Alloy etc
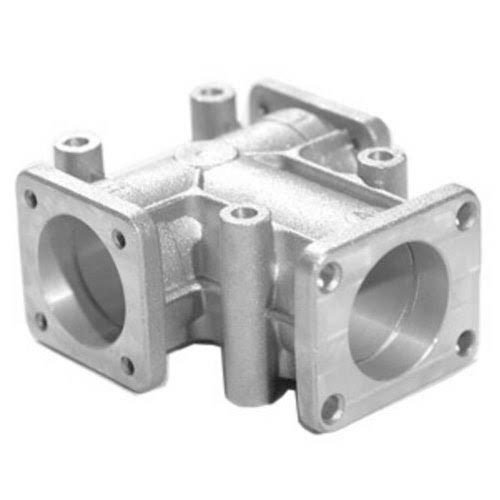
Zinc Alloy
Zinc is used to form numerous metal casting alloys, including brass, bronze, nickel silver, soft solder, German silver, spring brass, and aluminum solder. zinc casting is commonly used to make electrical, automotive, and hardware equipment. Due to decreased cost, zinc alloys are often the choice for larger items where a higher volume of materials is required to make a part.
- Zamak-2
- Zamak-3
- Zamak-4
- Zamak-5
- Zamak-7
- etc
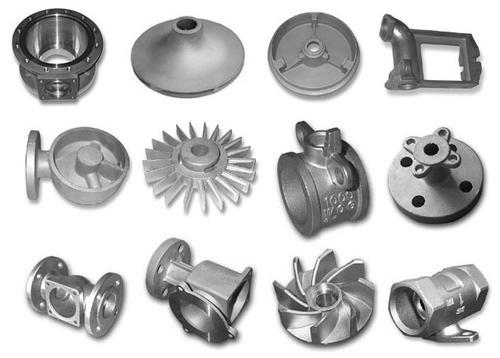
Magnesium alloy
Brass has desirable properties for a number of applications. It is low friction, has excellent electrical conductivity and has a golden (brass) appearance.
- AZ63
- AZ81
- AZ91
- AM50
- AM60
- ZK51
- ZK61
- ZE41
- ZC63
- HK31
- HZ32
- QE22
- QH21
- WE54
- WE43
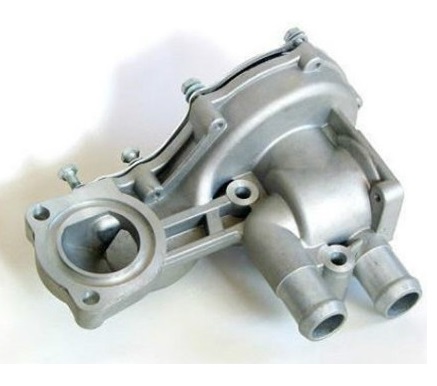
Steel
- 1045 Steel (45 #)
- 1008 Steel
- 1018 Steel
- 1020 Steel
- 1025 Steel
- 11Smn30 Steel
- 1215 Steel
- 4041 Steel
- 40Cr Steel
- 4130 Steel
- 4137 Steel
- 4140 Steel
- 42 Crmo Steel
- 4340 Steel
- 4J36 Steel Alloy
- 5140 Steel
- 5160 Steel
- 60Si2Mn Steel
- 65Mn Steel
- A2 Tool Steel
- A36 Steel
- C3600
- Class 8 Gray iron
- Cr12Mov Steel
- D2 mould steel
- DC-01 Steel Cold rolled steel
- EN16T Steel
- EN3B Steel
- EN8T Steel
- H13 Steel
- Inconel Steel
- Invar 36 Steel
- NAK80 Steel
- P20 Steel
- S136 Steel
- S7 Steel Tool Steel
- SK5 Steel
- SKD11 Steel
- SKD61 Steel
- SKH51 Steel
- ST37 (Q235) Steel
- ZGmn13-5
- Galvanized Steel / SGCC / SECC
- S7 Steel
- SCM440 (40CrMo) Steel alloy
- 52100 Bearing Steel
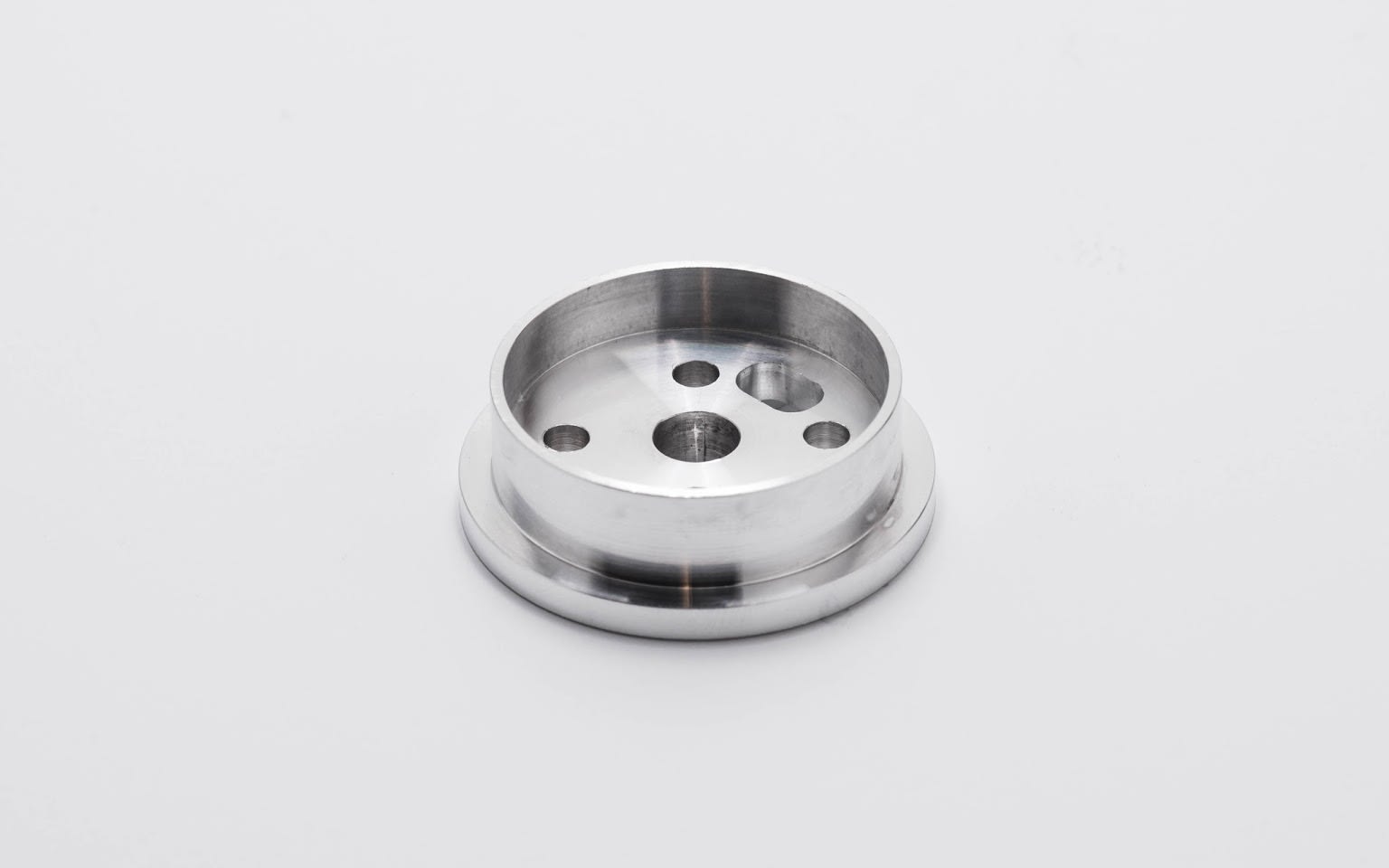
Stainless Steel
- SUS304 Stainless steel
- SUS303 Stainless steel
- SUS301 Stainless steel
- SUS316 Stainless steel
- SUS316L Stainless steel
- SUS401 Stainless steel
- SUS416L Stainless steel
- SUS416 Stainless steel
- SUS420 Stainless steel
- SUS201 Stainless steel
- SUS430 Stainless steel
- SUS431 Stainless steel
- SUS440C Stainless steel
- SUS410 Stainless steel
- SUS630 / 17-4PH Stainless steel
- PP631 / 17-7PH Stainless steel
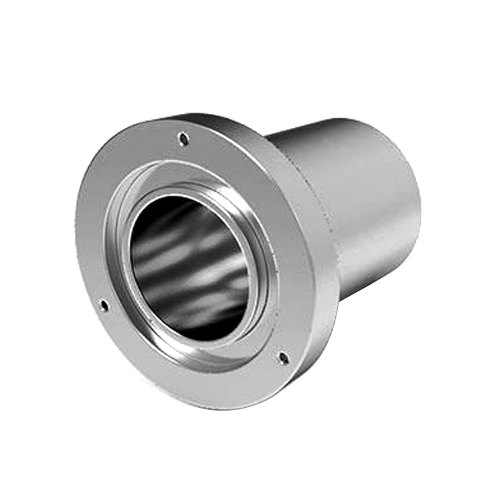
Titanium
- TC4 Titannium Alloy
- TC5 Titanium Alloy
- Military-grade titanium Alloy
- Food-grade titanium Alloy
- R53400 Titanium Alloy 9
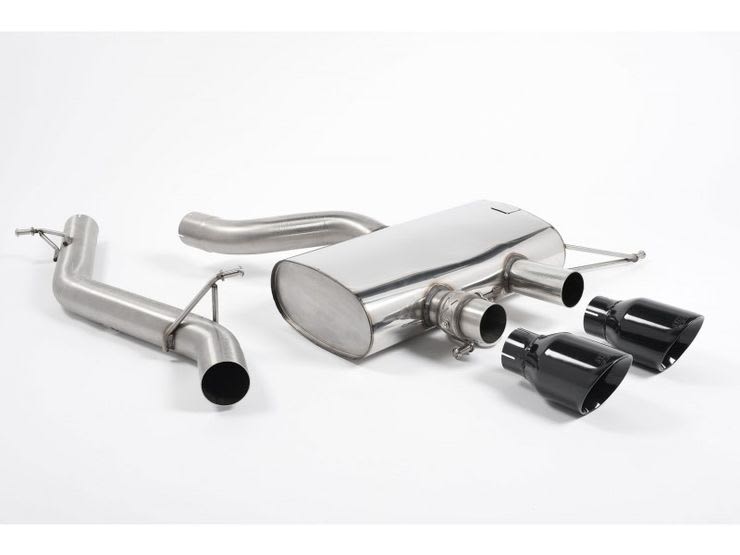
Plastics
- ABS
- PC
- ABS+PC
- PMMA
- POM
- PP
- PA
- PEEK
- PET
- PVC
- PPSU
- PPS
- PTFE
- PBT
- PE
- PEI
- HDPE
- UPE
- CPVC
- EPP
- FR-4
- HIPS
- LDPE
- PAI
- PETG
- PPA
- PS
- PVDF
- Bakelite

Standard Tolerances
If you do not provide us with your tolerances for High-Pressure Die Casting, we use standard tolerances DIN-1688. Tolerances can be greatly affected by part geometry and type of material. Our design engineers will consult you on every part of the project and will try to provide you with the highest degree of precision possible.
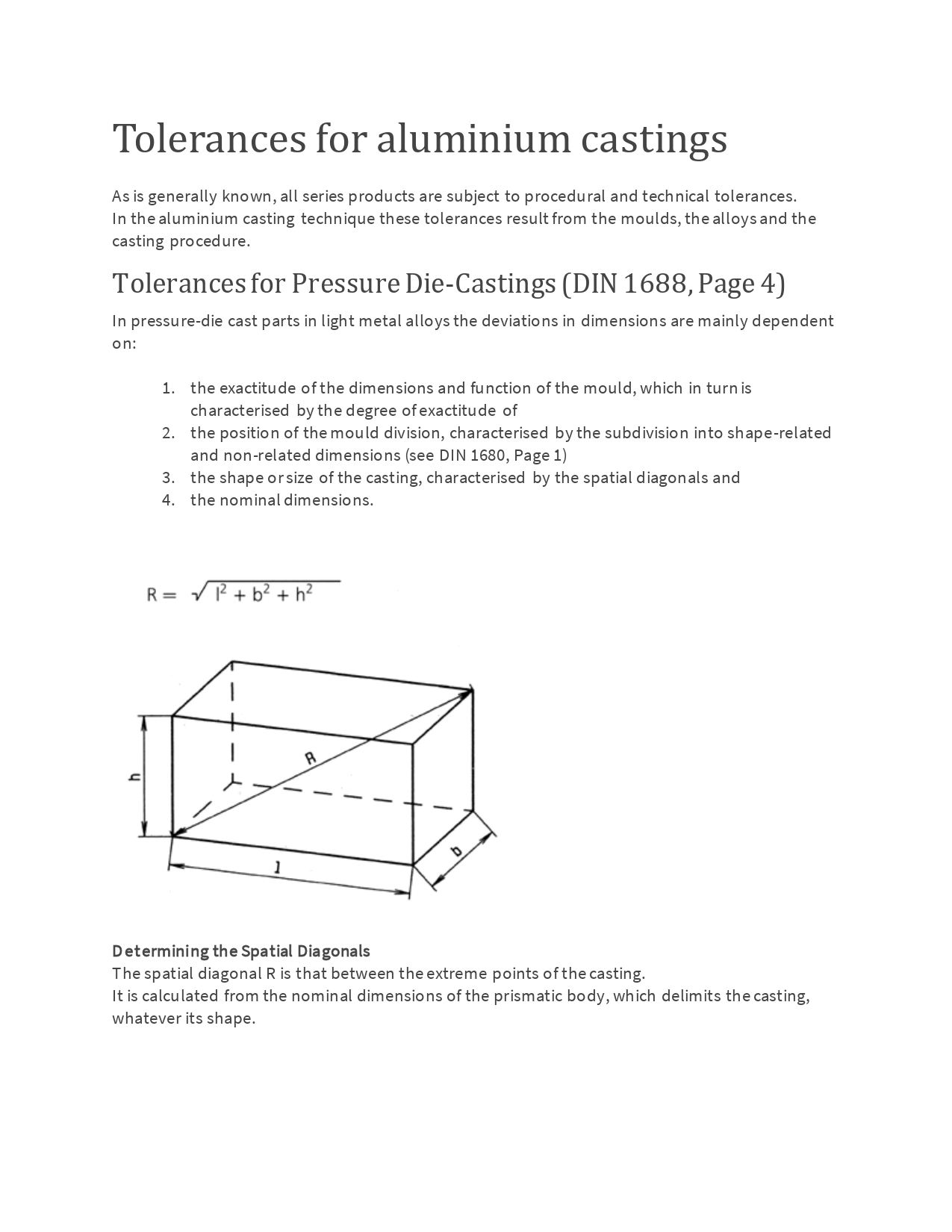
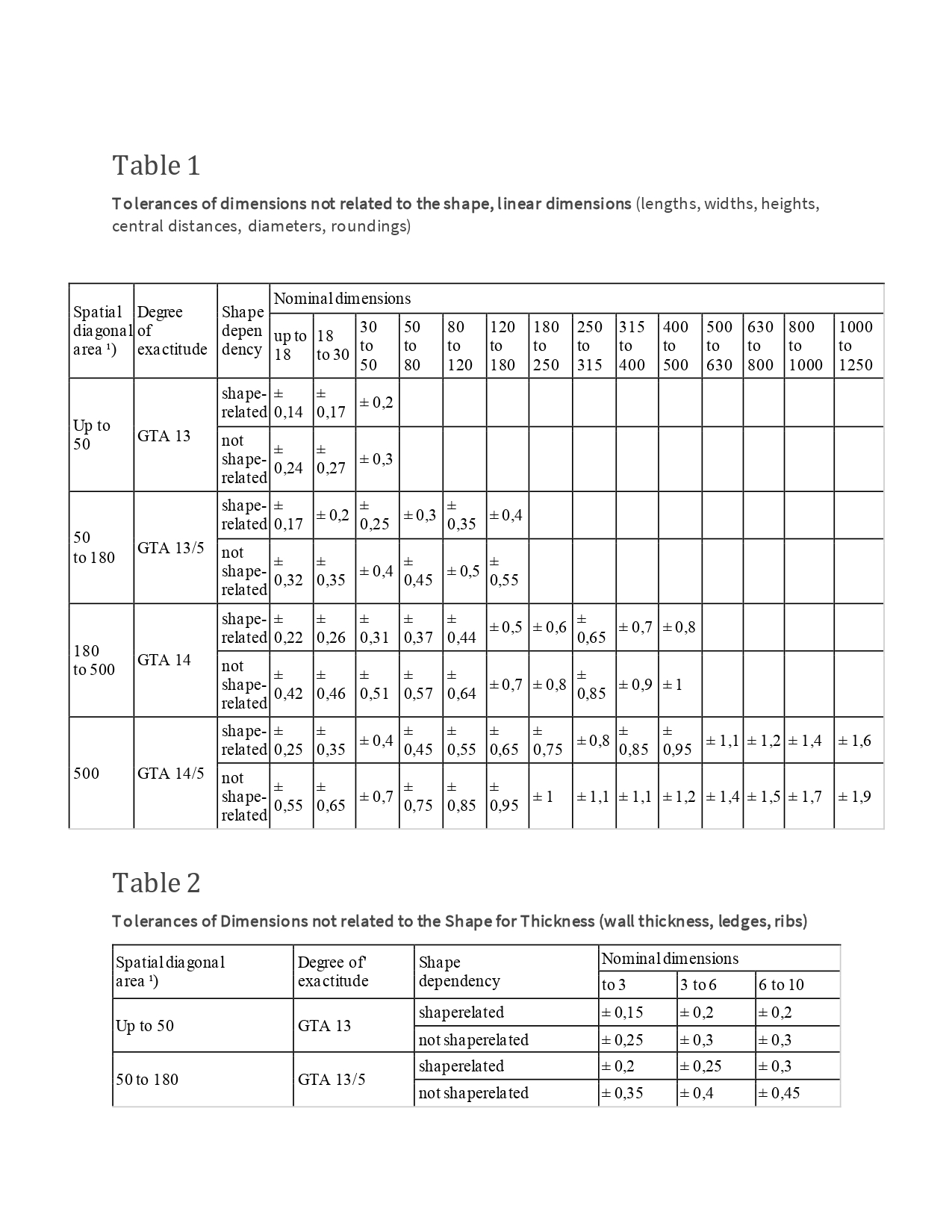
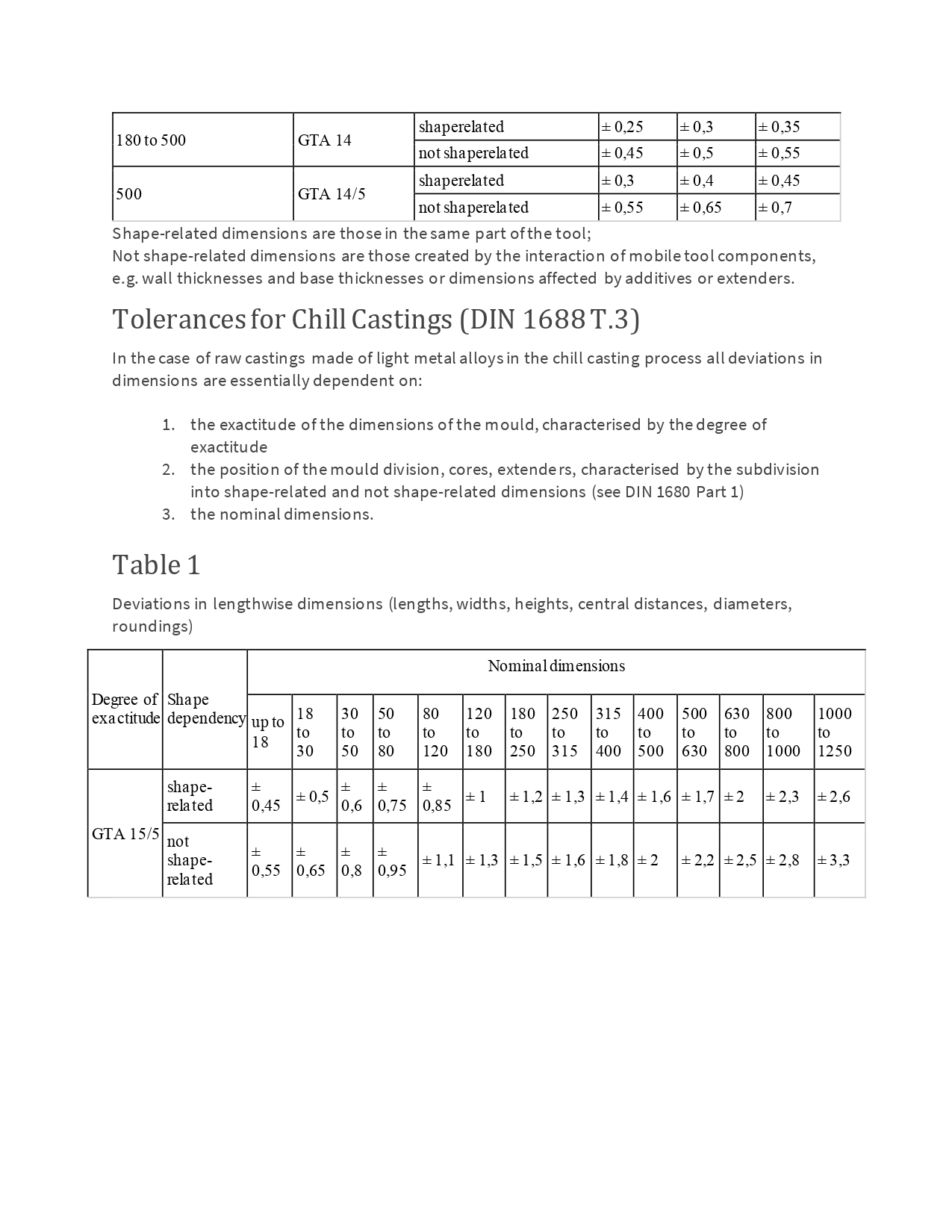
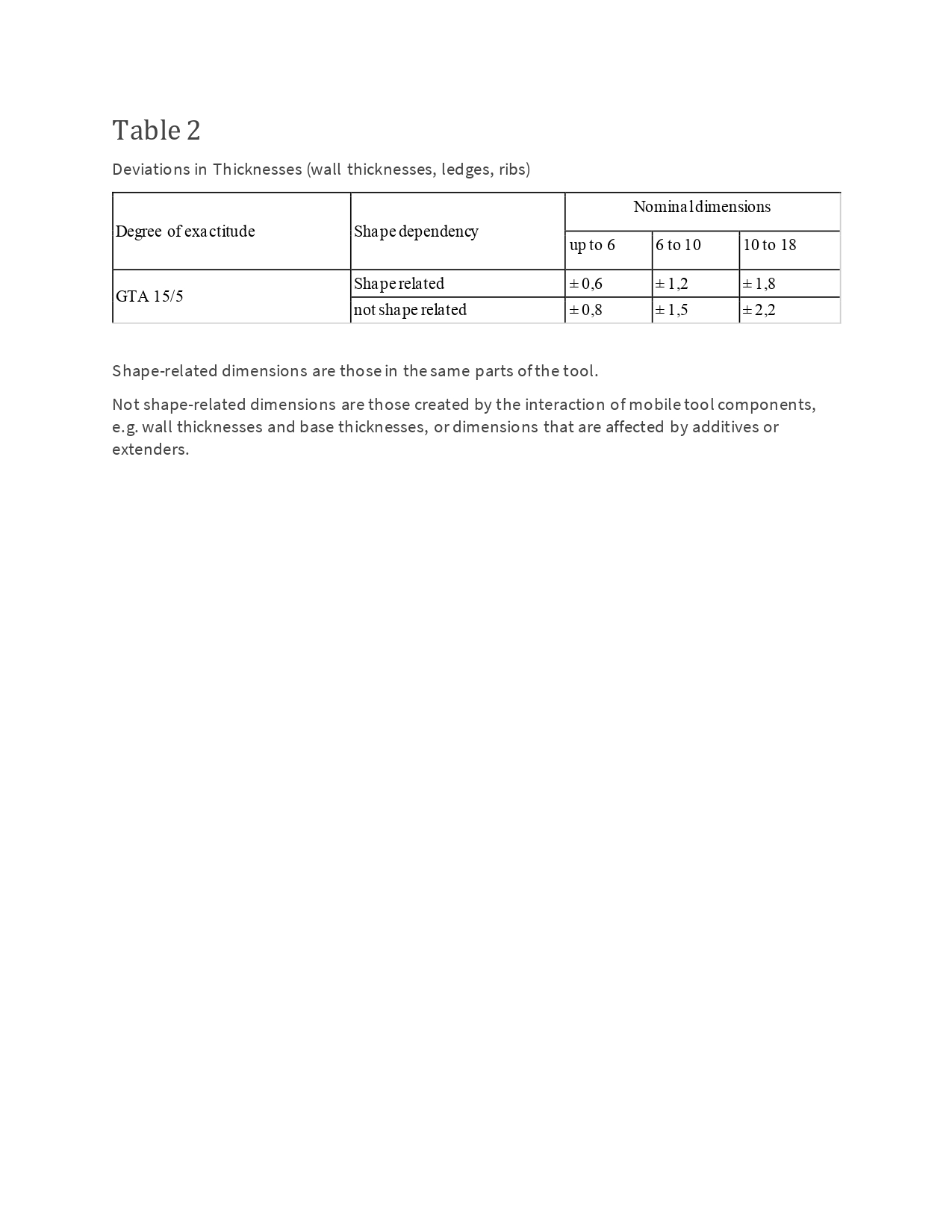
Finishes
Renderfact provides surface finishes on all Pressure Die Casting parts, including anodizing, electroplating, bead blasting, polishing, brushing, powder coating, and painting.
Anodizing improves corrosion resistance, enhancing wear resistance and hardness, and protecting the metal surface. Widely used in mechanical parts, aircraft, and automobile parts, precision instruments, etc.
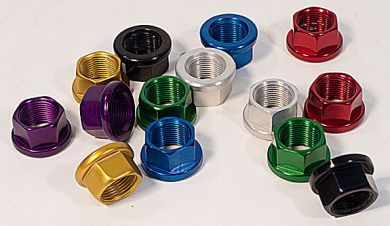
Bead blasting results in parts with a smooth surface with a matte texture. Used mainly for visual applications and can be followed by other surface treatments.
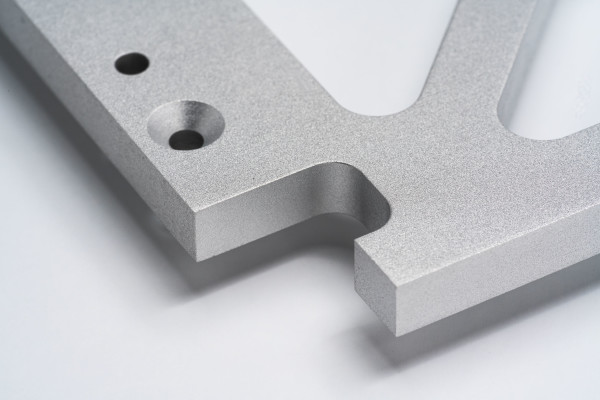
Powder coating forms a durable, wear resistant and corrosion resistant layer on the surface of parts. Powder coating can be used to apply colors to parts and is compatible with any metal.
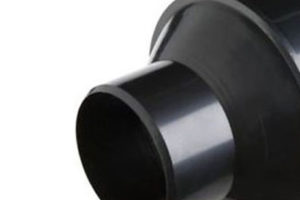
Electroplating can be functional, decorative or corrosion-related. Many industries use the process, including the automotive sector, in which chrome-plating of steel automobile parts is common.
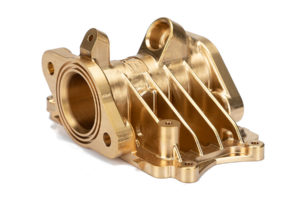
Polishing is the process of creating a smooth and shiny surface, either through physical rubbing of the part or by chemical interference. The process produces a surface with significant specular reflection, but in some materials is able to reduce diffuse reflection.
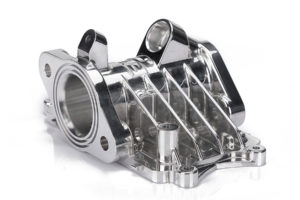
Brushing is a surface treatment process in which abrasive belts are used to draw traces on the surface of a material, usually for aesthetic purposes. Most commonly applied to aluminum.
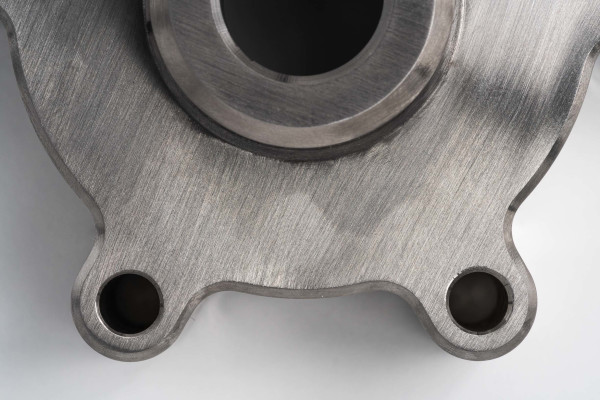
Painting the surface of a part improves its aesthetic appearance and can provide brand recognition to consumers. In addition, painting can have a protective effect on parts.
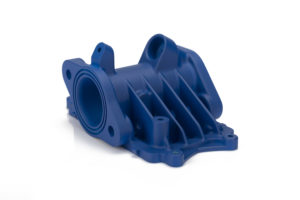
Applications
Rapid Tooling
Rapid tooling at Renderfact, you get to use the actual production grades of material, allowing you a much clearer picture of how the parts will act in real-world applications and enabling you to test and confirm you have made the correct material choices.
Rapid Prototyping
Rapid prototyping allows you to leverage the many advantages of computerized equipment to produce fast-turnaround prototypes, engineering models and high-quality end-use parts in the least possible time. Get in touch for your next rapid prototyping project.
End-Use Production
Renderfact is your ideal source for end use parts. Proven manufacturing processes like CNC Machining, and Injection Molding are complemented by our additive manufacturing capabilities like SLA, SLS, FDM, and DMLS, which provide you with incredible design freedom where complexity and small design iterations are not a roadblock.
Gallery
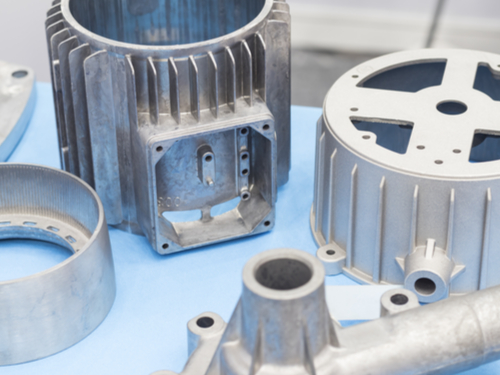
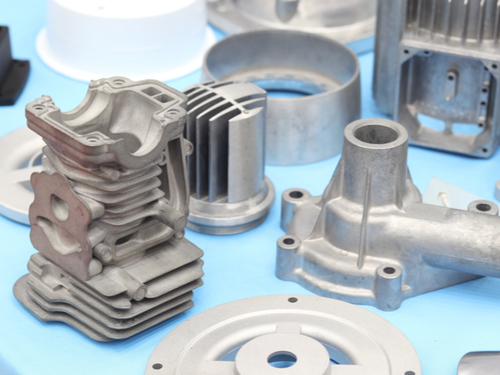
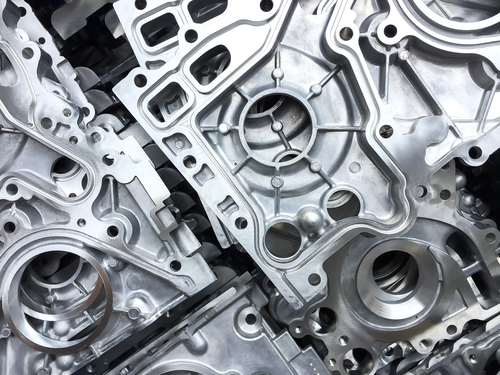
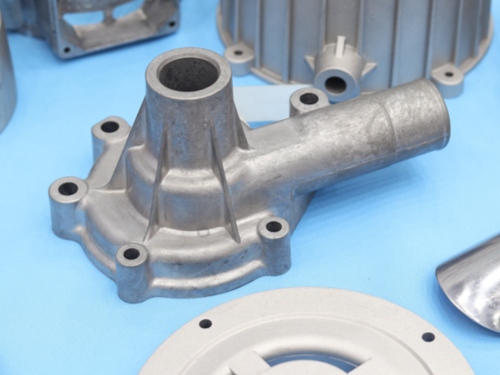
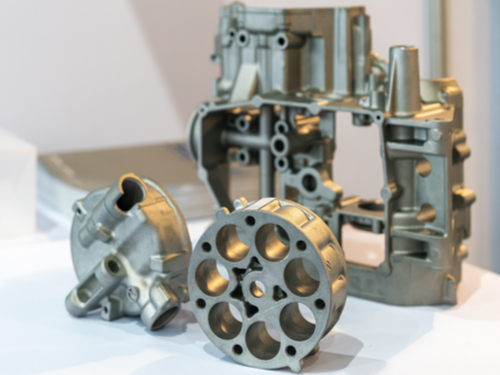
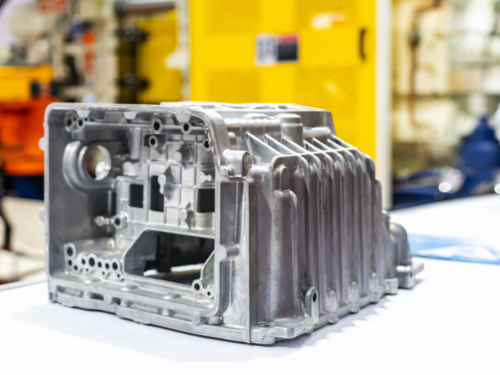
Quality Reports & Certifications
Full dimensional report
A Full work-up of dimensions can be provided for the parts you order for your peace of mind, on request.
Material certification
We have partnered with specialized Metallurgy Labs that provide and process special material certifications when requested.
First part verification
We provide first part verification services for a mutually agreed MOQ or on specific requests. We normally ship two sets of parts to the customer for verification and only once the parts have been validated, we move into full production.
Only 4 simple steps to complete your project. Follow the instruction and give it a try!